The cable bend radius is a term often encountered in the fields of electrical engineering, telecommunications, and cable manufacturing. It refers to the minimum radius one can bend a cable without causing damage to it. In today’s interconnected world, where cables are the lifeline for data transmission and power supply, understanding the concept of bend radius is crucial for maintaining the integrity and longevity of cables.
This article aims to provide an in-depth understanding of cable bend radius, the factors affecting it, and why adhering to this specification is critical for both safety and performance. We will also explore industry standards and best practices for managing cable bend radius in various applications.
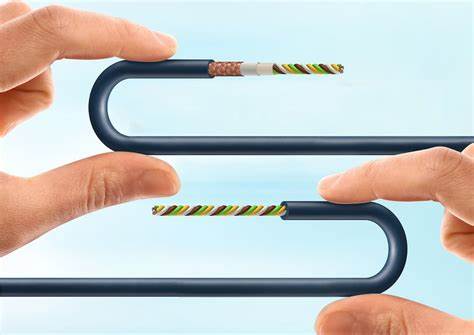
What is Cable Bend Radius?
Cable bend radius is a specification that defines the smallest radius a cable can be bent without incurring damage or degradation in performance. It is usually expressed in terms of the cable’s diameter. For example, if a cable has a bend radius of 10 times its diameter, it means that a 1 cm thick cable can be safely bent to a radius of 10 cm.
A bend radius smaller than the specified limit can cause various problems, including:
- Deformation of the cable jacket: This can expose the conductors inside, making the cable more vulnerable to damage and failure.
- Increased attenuation: Especially for fiber optic cables, exceeding the bend radius can lead to signal loss due to bending stress.
- Electrical degradation: Excessive bending in power cables can increase resistance, and heat generation, and even result in short circuits or electrical fires.
- Physical damage: Overly sharp bends can permanently damage the internal components of the cable, such as the insulation, conductors, and shielding.
Importance of Adhering to Bend Radius Specifications
When cables are installed improperly with bends tighter than the recommended bend radius, the risks extend beyond cable damage. Operational and safety issues can arise, which can be costly and dangerous.
- Safety Concerns: Power cables bent beyond their bend radius limit may have compromised insulation, leading to electrical fires or electrical shocks.
- Performance Degradation: Network cables and fiber optic cables bent too sharply can result in signal loss, reducing data transmission speeds and increasing error rates.
- Premature Cable Failure: For any kind of cable, an improper bend radius can reduce the life expectancy of the cable, necessitating frequent replacements and increasing maintenance costs.
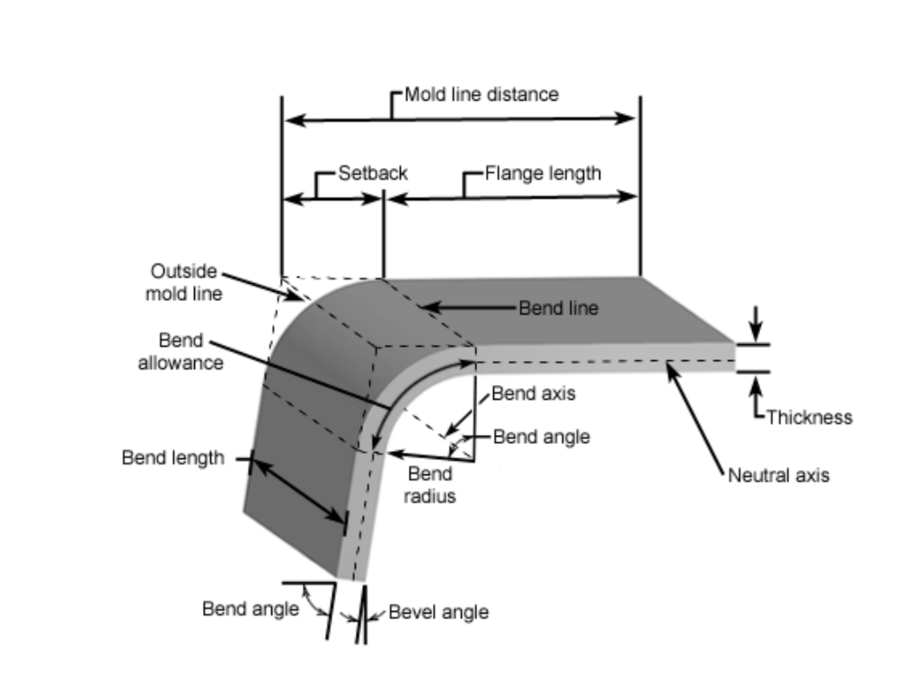
Understanding the correct bend radius for different types of cables can help avoid these issues, ensuring that both safety and performance standards are maintained.
Types of Cables and Their Bend Radius Requirements
Different types of cables have varying bend radius requirements, depending on their construction and use. Below are some of the most common types of cables and their typical bend radius specifications.
1. Fiber Optic Cables
Fiber optic cables are extremely sensitive to bending. Light traveling through the cable can escape or reflect improperly if bent beyond its specified bend radius, leading to signal loss (attenuation). Fiber optic cables typically require a bend radius of 10 to 20 times the cable’s diameter, depending on the cable type.
2. Ethernet Cables (Cat5, Cat6, Cat7)
Ethernet cables, commonly used in data networking, have a specified bend radius to ensure signal integrity. The bend radius for these cables is generally about four times the cable’s diameter. Exceeding the bend radius can lead to crosstalk and increased signal loss.
3. Coaxial Cables
Coaxial cables, used for TV and radio signal transmission, have a bend radius that typically ranges from six to ten times the cable diameter. Exceeding the bend radius may cause the internal dielectric and conductors to shift, affecting signal quality.
4. Power Cables
Power cables generally have a larger bend radius than data cables due to their size and construction. Depending on the insulation material and voltage rating, the bend radius for power cables can range from six to twelve times the cable diameter.
5. Control and Instrumentation Cables
Control and instrumentation cables, used in industrial applications, have varied bend radius requirements based on their design. The bend radius usually falls within six to ten times the diameter, with specific values determined by the cable’s shielding and insulation.
Factors That Affect the Bend Radius of a Cable
Several factors influence the bend radius of a cable. Understanding these factors can help in selecting the right cable for your application and ensure proper installation.
1. Cable Construction
The materials used to construct a cable play a significant role in determining its bend radius. Cables with more flexible materials, such as those made of rubber or silicone, will generally have a smaller bend radius. In contrast, cables with more rigid materials, like metal shielding, will have a larger bend radius.
a. Conductor Type
- Stranded Conductors: Cables with stranded conductors are more flexible than those with solid conductors. Stranded conductors consist of multiple smaller wires bundled together, making the cable more pliable and allowing for a smaller bend radius.
- Solid Conductors: Cables with solid conductors are less flexible and have a larger bend radius. These cables are often used for permanent installations, where flexibility is not a priority.
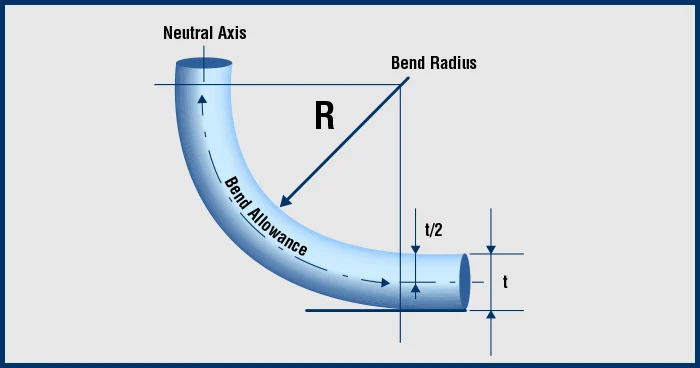
b. Insulation and Jacket Material
The type of insulation and outer jacket material can also impact the bend radius. Materials such as PVC (Polyvinyl Chloride) are more rigid, leading to a larger bend radius. On the other hand, materials like rubber or Teflon are more flexible and allow for tighter bends.
2. Cable Diameter
The size of the cable is directly proportional to its bend radius. Thicker cables require larger bend radii to avoid damage. For example, a thick power cable will need to be bent at a much larger radius than a thin fiber optic cable.
3. Temperature
Temperature changes can affect the flexibility of a cable. In colder environments, cables tend to become more rigid, which increases the required bend radius. Conversely, in warmer conditions, some cables become more flexible, allowing for tighter bends. It is essential to check the cable’s temperature rating and adjust the bend radius accordingly.
4. Type of Installation
Different types of installations also impact the bend radius. For example, when cables are installed in tight spaces or pulled through conduits, they may be subjected to additional stress that could reduce their flexibility, requiring a larger bend radius. Horizontal or vertical cable runs may also have different bend radius requirements, particularly in complex setups like data centers.
5. Tension on the Cable
When installing cables, tension must be taken into account. Excessive pulling or force applied during installation can reduce the effective bend radius of a cable. This is particularly important in long cable runs, where tension increases as more cable is pulled. Using proper installation techniques, such as applying lubricants or using pull boxes, can help maintain the appropriate bend radius.
6. Frequency and Type of Use
Cables that are regularly flexed, such as in robotics or industrial machinery, need to have a smaller bend radius to accommodate constant movement. For such applications, cables are designed with more flexible materials and stranded conductors, ensuring that they can withstand frequent bending without damage.
Industry Standards for Bend Radius
Several industry standards and guidelines help manufacturers and installers determine the appropriate bend radius for various cable types. Adhering to these standards ensures that cables are installed safely and function efficiently.
1. National Electrical Code (NEC)
The NEC provides guidelines for electrical installations, including specifications for cable bend radius. These codes are especially critical for power cables, where improper bends can pose significant safety risks.
2. Telecommunications Industry Association (TIA)
The TIA has established standards for bend radius in fiber optic and copper cables for telecommunications and data networking. These standards are designed to minimize signal loss and maintain network performance.
3. International Electrotechnical Commission (IEC)
The IEC sets international standards for electrical and electronic systems, including specifications for cable bend radius. These standards are particularly important for ensuring compatibility and safety in global installations.
4. Manufacturers’ Specifications
In addition to industry standards, individual cable manufacturers often provide specific bend radius recommendations for their products. It’s crucial to consult these guidelines during installation, as the manufacturer’s specifications are tailored to the cable’s unique construction and materials.
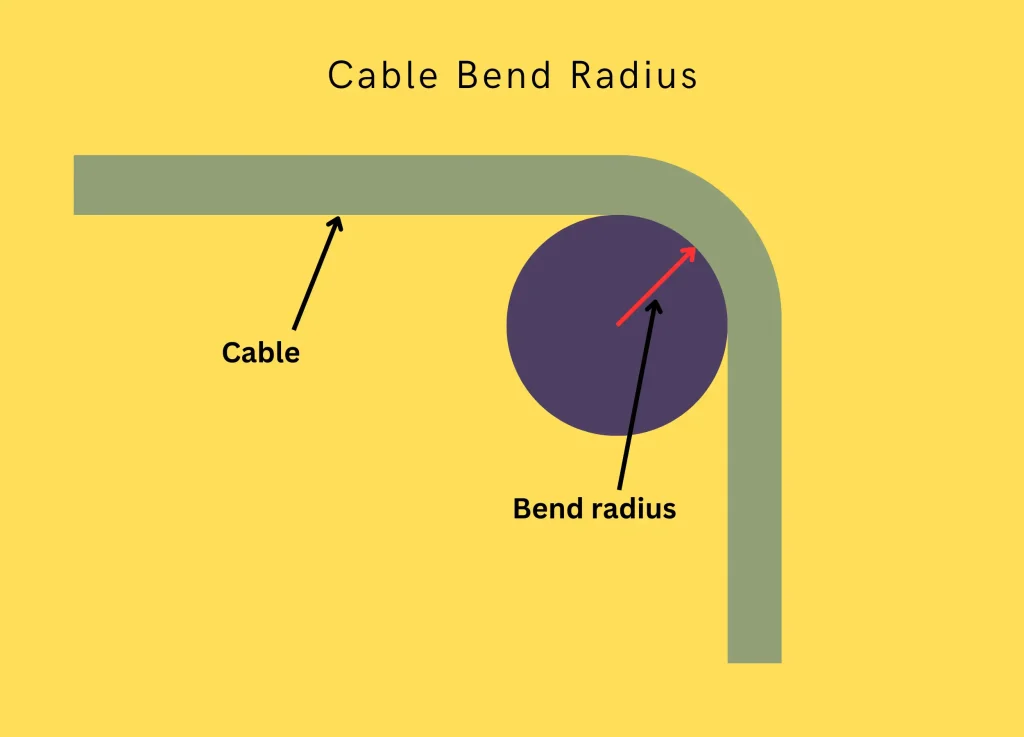
Best Practices for Managing Cable Bend Radius
Consider these best practices during installation and maintenance to avoid the pitfalls of exceeding a cable’s bend radius.
1. Plan Cable Runs Carefully
Before installation, map out the cable runs to minimize sharp bends and avoid tight spaces. Use tools like cable trays, conduits, or raceways to guide the cables and maintain the correct bend radius.
2. Use Cable Management Tools
Employ tools like cable ties, clips, and guides to help control the bending of cables, especially in dense installations. Cable management not only maintains the bend radius but also helps with overall organization.
3. Pull Cables with Care
Avoid excessive tension when pulling cables through conduits or other structures. Using a lubricant can help reduce friction, ensuring that the cable does not stretch or deform. Mechanical aids like pulleys or pull boxes can also help maintain the correct bend radius.
4. Consult Manufacturer Guidelines
Always follow the manufacturer’s guidelines for bend radius, as they are specific to each cable type. This is particularly important for high-performance cables, such as fiber optics or high-voltage power lines.
5. Inspect Cables Regularly
Over time, cables may shift or sag, leading to changes in their bend radius. Regular inspections can help identify cables that have been bent beyond their specifications, allowing for timely corrective action.
Understanding and adhering to the cable bend radius is essential for the longevity and performance of cables, whether in data centers, industrial settings, or home networks. By taking into account factors such as cable construction, diameter, temperature, and installation environment, you can ensure that your cables are installed correctly and remain safe to use. Following industry standards and best practices will also minimize the risks of cable damage, signal loss, and premature failure.
Whether you’re a professional installer or simply managing a home network, maintaining the appropriate bend radius for each cable will lead to better performance, improved safety, and longer-lasting installations.