Wire and Cable FAQs
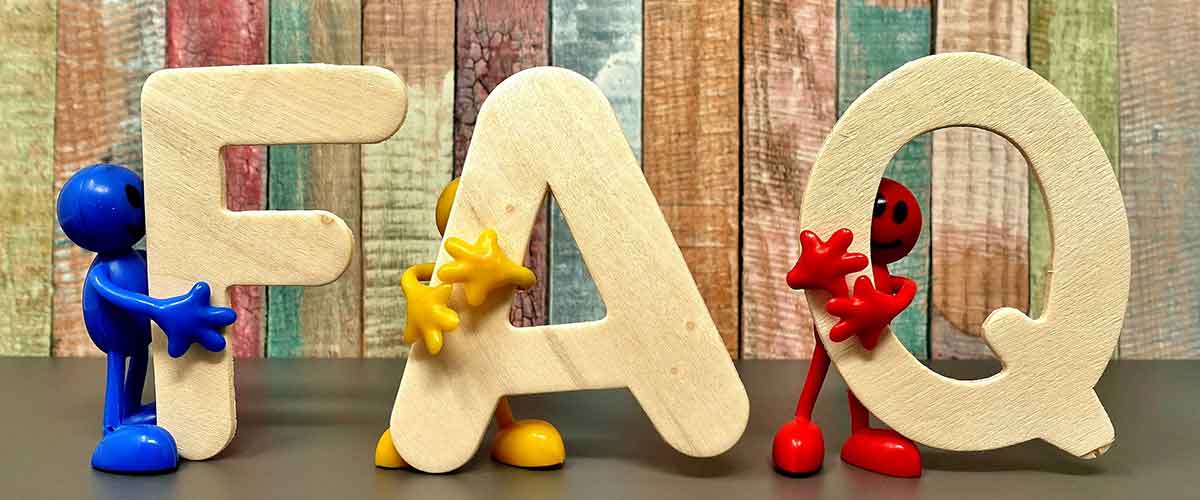
ZMS is a professional team in the cable industry. Our professional engineers have many years of experience in cable manufacturing and R&D. After years of experience in the cable industry, we have put together a series of wire and cable-related problems and solutions. We hope these FAQs will be of help.
Read More About Electrical Cable FAQs
1. Power supply system
Electric power system selection of wire and cable commodity specific airframe bare cable line, busbar (bus bar), wire and cable (plastic cable line, oil paper force cable (basically replaced by plastic wire and cable), rubber cable line, airframe insulated cable line), branch cable line (to replace part of the bus bar), electromagnetic wire and its electrical equipment with electrical weapons equipment wire and cable.
2. Information content transmission system
The key wire and cables used for information content transmission systems are municipal telephone cable, television cable, electronic device cable, radio frequency cable, metal cable, data cable, electromagnetic cable, power engineering communication, or another composite cable, etc.
3. Industrial equipment, instrumentation equipment system
This part of the bare cable line in addition to the airframe almost other commodities are used, but mainly wire and cable, electromagnetic wire, data cable, instrumentation equipment cable line, etc.
Power cables are cables used for the transmission and distribution of electrical energy, power cables are commonly used in urban underground power grids, power station lead-in lines, internal power supply of industrial and mining enterprises, and underwater transmission lines across rivers and seas.
In the power lines, the proportion of cables is gradually increasing. Power cables are cable products used to transmit and distribute high-power electrical energy in the backbone of the power system, including 1-500KV and various voltage levels above, and various insulation of power cables.
There are many different types of wire and cable. They are mainly defined by their conductors. Either copper or aluminum, or stranded or solid. However, many different types of power cables are designed for specific applications.
Common types of wire and cable include low, medium, and high voltage power cables, control cables, overhead cables, overhead fiber optic cables, submarine cables, fire resistant cables, armored cables, etc.
Power cables are used in the electric utility, industrial and commercial markets.
These cables are available in a variety of constructions, materials, and ratings to meet the needs of a wide range of applications.
Power cables can be used for overhead, bare, and direct burial wiring. Many are also suitable for heavy-duty use.
Cable Conductors
The cable conductor is a current-carrying element made of aluminum or copper with a specific cross-section of specified ratings and a resistance/km within certain specified ranges.
Electrical Insulation
Cable insulation is provided on the conductors to keep them electrically isolated from each other. The various insulation materials used are PVC, XLPE (cross-linked polyethylene), rubber, etc.
The insulated conductors are called cores. Cables may have one or more cores. In multi-core cables, the cores are spirally twisted together. In two-core, three-core, and multi-core cables, the cores are laid together at the appropriate twist spacing. The outermost layer is laid in the right direction and subsequent layers are laid in the opposite laying direction.
Inner Sheath
Stranded core cables are equipped with an inner sheath, which can be applied by extrusion or twisting. Make sure that the shape is as round as possible. The inner sheath is applied so that it fits snugly over the laid core and should be removable without damaging the insulation. The thickness of the inner sheath is specified in the relevant standards and is based on the calculated diameter of the laminated core.
Cable Armoring
A wire, strip, or tape wrapped in a spiral around a cable to protect it from sharp objects, crushing forces, and damage from rodents or bored insects is called armoring.
In the case of single-core cables, the armoring is on the insulation, and in the case of two-core, three-core, and multi-core cables, the armoring is on the inner sheath.
Outer Sheath
The outer sheath is usually an extruded plastic cover over a laminated or armored core. PVC is a common sheath material. The outer sheath provides mechanical, thermal, chemical, and environmental protection. There are no electrical functions assigned to the outer sheath. The color of the outer sheath is typically black.
Based on voltage ratings, such as low-voltage, high-voltage, and ultra-high-voltage cables.
Based on conductor material, copper conductor or aluminum conductor.
Insulation material is PVC insulation, rubber insulation, cross-linked polyethylene insulation, etc.
Armored or non-armored cables.
According to the sheath material, such as PVC sheath, XLPE sheath, rubber sheath, lead sheath, aluminum sheath, etc.
Based on the number of cores, such as single-core, two-core, three-core, three-and-a-half-core, four-core, multi-core, etc.
Based on the cross-section of the conductor.
Based on the type of conductor, solid, stranded, scalloped, etc.
As is evident from the above, the type of cable will vary greatly depending on the various factors involved. To facilitate the identification and description of cable types, some form of type designation is usually used.
According to GB/T3956-1997, there are four types of conductors, the first, the second, the fifth, and the sixth. The first one is a solid conductor, and the second one is a stranded conductor. The first kind and the second kind are intended for conductors of fixed laying cables, the fifth kind and the sixth kind are intended for conductors of flexible cables and flexible wires, and the sixth kind is softer than the fifth kind.
1. Solid conductor
Conductor material with metal-plated or non-metal-plated annealed copper wire, uncoated aluminum, or aluminum alloy wire.
Solid copper conductors should be round cross-sections, 25 and above solid copper conductors are only intended for special cables, but not for general cables.
Solid aluminum conductors, cross-sections 16 and below should be a round cross-section, 25 and above, if a single-core cable should be a round cross-section, if a multi-core cable, can be a round or formed cross-section.
2. Stranded conductors
To increase the flexibility or curvature of the cable, a larger cross-section of the cable core by multiple smaller diameter single wire stranded. The core of multiple single wire stranded wire is flexible and bendable.
For core bending, the core center line inside and outside the two parts can move to compensate for each other, bending will not cause plastic deformation of the conductor, so the flexibility and stability of the core are greatly improved.
2.1 Non-compact stranded round conductor
The stranded round aluminum conductor cross-section is generally not less than 10mm2. a single line in the conductor should have the same nominal diameter, the conductor’s single line root, DC resistance should be in line with the standard provisions.
2.2 Tightly stranded round conductor and creating conductor
Tightly stranded round aluminum conductor cross-section should be not less than 16mm2, stranded copper or aluminum conductor cross-section should be not less than 25mm2, the same conductor in two different single line diameter ratios should not exceed 2, the number of single line conductor and DC resistance should be in line with the standard provisions.
3. Soft conductor (the fifth and sixth)
The conductor should be metal-plated and not metal-plated annealed copper wire composition.
The single line in the conductor should have the same nominal diameter.
The diameter of the single wire in the conductor shall not exceed the specified maximum value, and the sixth conductor is finer than the diameter of the single wire in the fifth conductor.
The conductor resistance should not exceed the maximum value specified by the standard.
The insulation layer of the cable is used to isolate the multi-core conductors from each other and the conductor and sheath, and to ensure a certain electrical voltage strength. It should have certain heat resistance and stable insulation quality.
The materials of the insulation layer are mainly oil-impregnated cable paper, plastic, and rubber.
According to the different materials used in the conductor insulation layer, the cable is mainly divided into plastic-insulated cable, rubber-insulated cable, and oil-impregnated paper-insulated cable. Insulation materials are classified as thermoplastic or thermosetting.
Thermoplastic materials lose their shape when heated. Despite heating, thermosetting materials retain their shape. The various insulation materials used are: PVC, XLPE, rubber, impregnated paper, etc.
- High dielectric strength
- Low dielectric constant
- Good mechanical properties
- Anti-aging
- High-temperature resistance
1. Plastic insulation
Plastic insulation mainly has two kinds of polyvinyl chloride insulation (PVC insulation) and cross-linked polyethylene insulation (XLPE insulation), and the cable insulation layer is made of thermoplastic extrusion and cross-linked by adding cross-linking agent after extrusion of thermoplastic polyethylene plastic. This insulation has good electrical properties and water resistance and can resist acid and alkali and corrosion, it also has the advantages of high allowable working temperature, good mechanical properties, and can manufacture high voltage cables.
XLPE Insulation
Cross-linked polyethylene (XLPE) is a thermosetting material. It is made by laminating PE (polyethylene) with cross-linking agents such as organic peroxides. The polyethylene molecules are “cross-linked” and form an interconnected network. The terms “curing” and “vulcanization” are also used for “cross-linking”.
PVC Insulation
Polyvinyl chloride (PVC or vinyl) is a thermoplastic, and PVC compounds are the standard insulation material for cables rated at 11,000 volts or less, as well as sheathing for the entire cable range.
PVC has good electrical properties. It is tough and resistant to flame, moisture, and abrasion. It is also sufficiently resistant to ozone, acids, alkalis, alcohols, and most solvents. PVC is resistant to oil and gasoline.
2. Rubber Insulation
Rubber-insulated power cables are insulated with styrene-butadiene rubber or synthetic rubber (ethylene propylene rubber, butyl rubber).
The outstanding advantage of this cable is that it is soft and flexible, which makes it especially suitable for mobile power and electricity supply installations.
However, the rubber insulation will be damaged quickly when it encounters oil: under the action of high voltage, it is easily cracked by the corona effect.
Therefore, this kind of cable is generally used for 10kV and below, while synthetic ethylene propylene rubber insulated cable can be used up to 35kV voltage level.
3. Oil-impregnated paper insulation
Oil-impregnated paper insulation consists of a combination of cable paper and impregnating agent.
Ordinary oil-impregnated paper insulation cable paper thickness of 0.08, 0.12, 0.17mm three; an impregnating agent with low-voltage cable oil and rosin mixture, known as viscous immersion cable oil.
In general. The thickness of the insulation layer is related to the working voltage. In general, the higher the voltage level, the thicker the thickness of the insulation layer, but not proportionally.
Because of the electric field strength considerations, the same voltage level of the cable when the conductor cross-sectional area is large, the thickness of the insulation layer can be thinner.
For cables of lower voltage levels, especially the oil-impregnated paper insulated cables of lower voltage levels, to ensure that the paper layer has a certain mechanical strength when the cable is bent, the thickness of the insulation layer is thickened with the increase of the conductor cross-section.
The shielding role of the cable is important for the cable.
Because the current through the wire and cable will be relatively large, the current around the magnetic field will be generated, so in order not to affect other components, plus shielding layer can be shielded from this electromagnetic field in the cable. It can play a certain role in grounding protection.
If breakage occurs within the cable core, the leakage of current can flow along the shielding layer such as the grounding network, playing a role in the safety protection by shielding silicone wire’s outermost layer of silicone rubber insulation layer.
Its role is to insulate while also protecting the wire and cable from internal damage, thus ensuring the safety of the cable in the process of use.
The shielding of the cable can play a certain role in grounding protection. If breakage occurs within the cable core, the leakage of current can flow into the grounding network along the shield. The role of safety protection with shielding silicone wire is the outermost layer of silicone rubber insulation layer.
Its role is to insulate while also protecting the wire and cable from internal damage, thus ensuring the safety of the cable in the process of use.
1. The rated voltage of the cable should be greater than or equal to the rated voltage of the power supply system at the installation point.
2. The continuous allowable current of the cable should be equal to or greater than the maximum continuous current of the supply load.
3. The core cross-section should meet the requirements of the stability of the power supply system in case of a short circuit.
4. The voltage drop is verified to meet the requirements according to the cable length.
5. The minimum short-circuits current at the end of the line should enable the protective device to operate reliably.
Wire and cable products are used in different applications, so the performance requirements are multifaceted and very extensive. As a whole, its main performance is integrated as follows.
1. Electrical performance
Electrical conductivity — most products require good electrical conductivity, and individual products require a certain range of resistance.
Electrical insulation properties – insulation resistance, dielectric coefficient, dielectric loss, electrical resistance characteristics, etc.
Transmission characteristics – refer to high-frequency transmission characteristics, anti-interference characteristics, etc.
2. Mechanical properties
Refers to tensile strength, elongation, bendability, elasticity, flexibility, vibration resistance, wear resistance, resistance to mechanical force impact, etc.
3. Thermal performance
Refers to the product’s temperature level, working temperature power transmission wire and cable heat generation and heat dissipation characteristics, load capacity, short circuit, and overload capacity, thermal deformation of synthetic materials and thermal shock resistance, thermal expansion of materials, and impregnation or coating material drip performance.
4. Corrosion and weather resistance
Refers to electrochemical corrosion resistance, resistance to biological and bacterial erosion, chemical resistance (oil, acid, alkali, chemical solvents, etc.) erosion, salt spray resistance, light resistance, cold resistance, mold resistance, and moisture resistance performance.
5. Aging performance
Refers to mechanical stress, electrical stress, thermal stress, and various other external factors, or the role of external climatic conditions, the product, and its constituent materials to maintain its original performance.
6. Other properties
Including the characteristics of some materials (such as the hardness of metal materials, creep, and polymer materials compatibility) and certain special characteristics of the use of products (such as non-delayed combustion, atomic radiation resistance, insect bite, delayed transmission, and energy damping, etc.).
Product performance requirements, mainly from the use of each specific product, the conditions of use, as well as supporting the relationship between the equipment and other aspects of the proposed.
In a product of the performance requirements, there are bound to be some of the main, decisive roles, that should be strictly required. Some are subordinate. Sometimes certain factors are constrained by each other. Therefore, a comprehensive study and analysis must be considered.
DC cables have the following characteristics compared to AC cables
1. The system used is different. DC cables are used in rectified DC transmission systems, while AC cables are commonly used in industrial frequency (domestic 50 Hz) power systems.
2. Compared with AC cables, DC cables have less power loss in the transmission process. DC cable power loss is mainly conductor DC resistance loss, insulation loss part is smaller (size depending on the size of the current fluctuations after rectification). And low-voltage AC cable AC resistance is slightly larger than DC resistance, high-voltage cable is very obvious, mainly because of the proximity effect and skin effect, insulation resistance loss accounts for a larger proportion of the impedance generated mainly by capacitance and inductance.
3. High transmission efficiency, and small line losses.
4. It is convenient to adjust the current and change the direction of the power transmission.
5. Although the price of the converter equipment is higher than the transformer, the cable line use cost is much lower than the AC cable. DC cable for positive and negative poles, simple structure. AC cable for three-phase four-wire or five-wire system, high insulation safety requirements, more complex structure, cable cost is more than three times the DC power cable.
6. DC cables are safe to use.
6.1 DC transmission inherent characteristics, it is difficult to generate induction currents and leakage currents, the same laying of other cables will not produce electric field interference.
6.2 Single-core laying cable will not affect the cable transmission performance due to the hysteresis loss of steel bridges.
6.4 The same voltage of direct and AC electric field applied to the insulation, DC electric field is much safer than AC electric field.
7. DC cables are simple to install and maintain, and they are less expensive.
The distinction in use
1. the direction of the current is different: alternating current is flowing out in two directions and then flowing back, and the size of both are in constant change, with the frequency is to indicate the direction of alternating current change fast or slow, and with the phase is to indicate the starting time of alternating current transmission. DC is only one direction, that is, the current can only start from the positive pole and flow to the negative pole.
2. different uses: our common life lights, motors, etc. are used in the alternating current. And DC is mainly used in various electronic instruments, electrolysis, electroplating, DC power dragging, etc.
3. output voltage is different: DC is a DC power supply, commonly used generally 30V, 6.0V, 9 0V, 12V, and several other common voltages, while the output voltage of AC is only 220V and 380V.
XLPE cable has a higher load capacity, stronger overload capability, and longer service life compared with PVC cable (PVC cable thermal life is generally 20 years when the environment is good, while XLPE cable thermal life is generally 40 years).
PVC decomposes and releases a lot of black smoke and toxic gas when it burns, while XLPE does not produce halogen toxic gas when it burns, and the superiority of cross-linked cables is increasingly recognized by the design and use departments.
Strengthen the analysis of common faults in power cables of transmission lines during the operation of the power system. And take effective measures to strengthen the hidden danger investigation, greatly reduce the occurrence of accident risks and the adverse effects brought about, and to better enhance the economic and social benefits.
At present in the power system transmission line power cable maintenance management process, by human, environmental and other factors transmission line power cable faults are also more.
So should strengthen the transmission power fault analysis and maintenance work, to greatly reduce the occurrence of accidents.
First, the causes of cable faults.
Understanding the causes of cable fault generation is conducive to reducing the incidence of faults and quickly eliminating cable faults.
Cable faults occur for the following reasons.
1. Mechanical damage.
2. Installation touch squeeze, excessive bending.
3. External damage formed by the operation on the cable path.
4. Strong ground vibration or impact external force caused by the fatigue breakage of the lead (aluminum) package.
5. Natural force damage. Such as land subsidence, road subsidence, etc.
6. Electrical and chemical corrosion of the cable sheath: the presence of a strong electric power field near the cable or acid and alkali operating area often makes the cable in a long-term corrosive environment resulting in insulation damage.
7. Loss of cable insulation: the laying of oil-impregnated paper cables with high and low undulation drop, will make the lack of oil parts insulation strength decline.
8. Poor craftsmanship and wet environment for the head, or do not lay the cable according to technical requirements.
9. Long-term overload operation of the cable causes the cable to overheat, which accelerates insulation aging.
10. Lightning strikes and line faults cause overvoltage breakdown.
The second is the cable fault classification.
For power cable failure, the severity of the damage varies greatly, we are here from the point of view of finding the cable fault point to classify.
1. Single-point fault: the fault is a point in the cable, whether it is single to ground, phase to phase and to ground, or mixed type of fault most cable faults are single-point faults.
2. Multi-point fault: as opposed to a single-point fault, a multi-point fault refers to the same cable with multiple fault points at different distances from the test end, which is also commonly seen in practice, mostly in low-voltage cables.
3. Large area and long-distance fault: relative to the point of fault in the cable, large area fault usually refers to a section of the cable in the insulation layer damage, such as the common cable in the large area of moisture failure.
4. Quality problems: This originally did not belong to the classification of cable faults. But in practice the application often found some user’s cable in the use of a very short period, there is a whole cable of the main insulation layer of the dielectric strength decline, leakage current is very large, manifested as a leaky fault situation.
Users in the field sometimes difficult to distinguish the point of failure or quality problems. Typical quality problems include insufficient dielectric strength of the insulation layer, uneven insulation layer, poor quality of steel armor, etc.
1. Low resistivity: The resistivity of aluminum-core cables is about 1.68 times higher than that of copper-core cables.
2. Good ductility: the ductility of copper alloy is 20~40%, and the ductility of copper for an electrician is more than 30%, while the aluminum alloy is only 18%.
3. High strength: the allowable stress at room temperature is 7~28% higher for copper than aluminum. Especially the stress under high temperatures, the difference between the two is very far.
4. Fatigue resistance: aluminum is easy to break after repeated bending, and copper is not easy. For elasticity indicators, copper is also higher than aluminum about 1.7 ~ 1.8 times.
5. Good stability, and corrosion resistance: copper core oxidation, and corrosion resistance, while the aluminum core is susceptible to oxidation and corrosion.
6. High capacity: due to low resistivity, the same cross-section of copper-core cable as aluminum-core cable allows the capacity (which can pass the maximum current) to be about 30% higher
7. Low voltage loss: due to the low resistivity of copper-core cable, the same section is in the case of the same current flow. Copper-core cables have a small voltage drop. The same transmission distance, to ensure higher voltage quality; under the conditions of the allowable voltage drop, copper-core cable transmission can reach a greater distance, that is, a large power supply coverage area, which is conducive to the planning of the network, reducing the number of power supply points set.
8. Low heat temperature: At the same current, the heat generation of copper-core cables of the same cross-section is much smaller than that of aluminum-core cables, making the operation safer.
9. Low energy consumption: Due to the low resistivity of copper, it is obvious that copper cables have low power loss compared to aluminum cables. This helps to improve the utilization rate of power generation and protect the environment.
10. Anti-oxidation, and corrosion resistance: copper-core cable connector performance is stable, and will not occur due to oxidation accidents.
11. Convenient construction: The copper core is flexible and allows a small radius of bend, so it is convenient to turn and easy to thread the pipe.
The cable is usually installed on a wooden/steel reel. The flange of the reel is painted with an arrow indicating the direction in which the reel rolls. If the drum rolls in the opposite direction, the cable will unwind and become loose.
All drums should be stored in such a way that sufficient space is left between them for air circulation. Under no circumstances should drums be stored “flat”, i.e. with the flange horizontal.
At present, the global market can be very many cable manufacturers, including formal, informal, and large manufacturers, there are small manufacturers, national standards, and non-standard. Therefore, when purchasing and using wire and cable, the quality of the wire and cable should be considered. What to pay attention to when purchasing wire and cable? The ZMS cable team has summarized the following points for your reference.
Product quality aspects
1. Choose the cable must look at the visibility. We must buy cables to choose the famous cable factory, some unknown small factory, it is not clear that their bottom line. If the production of the cable shortage, the last to suffer or their own.
2. Look at the certificate of conformity. National standard cables have corresponding certificate information, including factory name, address, specifications, voltage, and other information. There should even be relevant inspection certificates and reports, etc.
3. To see if there is an international certification mark. Because wire and cable products are national mandatory safety certification products, if there is no such certification mark, must be unqualified.
Product performance
1. Load capacity
The selection of cable models must have a sufficient load, otherwise, when the wire load power supply, is coupled with the hot weather, it is easy to fire.
2. Waterproof ability
Some cables and wires are buried underground, when it rains, if the cable is broken, it is very easy to cause a short circuit and leakage situation, which may cause casualties.
3. Electrical conductivity
Many people use copper-containing magazines or scrap copper to save costs, which greatly reduces the electrical conductivity of the cable.
4. Length
Length This is one of the tricks often used in jerry-building, someone will say, I bought the wire labeled above the number of meters, look at the 100 meters, you should pay attention, he has a meter label, but in the middle part, some crooks but undercount 10 meters. For example, 30 meters and then start marking 40 meters.
Therefore, it can be seen that although a small cable, there are many pits inside, the purchase of wire and cable to pay attention to these matters, to avoid causing unnecessary losses to themselves.
For circuits with voltage levels of 1kV and below, 1-5 core cables can be selected according to different grounding safety requirements.
For medium and high-voltage three-phase power supply circuits, when the working current is larger or the cable is laid underwater, 3 single-core cables can be selected for each circuit. In addition to the above-mentioned cases, 3 core cables should be used.
For high-voltage, AC single-phase power supply circuits such as electrified railroads, a 2-core cable or 2 single-core cables should be used for each circuit.
For a high-voltage DC transmission system, a single-core cable should be used.
Flame-retardant cables have self-extinguishing properties, are difficult to burn can make the fire not produce the spread of a variety of other equipment, to avoid causing greater losses.
Fire-resistant cables are cables that can maintain safe operation for a certain period in the event of combustion. Fire-resistant cables are mostly used as emergency power supply circuits to ensure the normal operation of the circuit in case of fire.
Fire-resistant cables are much safer. Generally speaking, fire-resistant cables can replace fire-retardant cables, but fire-retardant cables cannot replace fire-resistant cables.
Long transmission distance: fiber optic connection distance up to 70 km.
Fast transmission speed: fiber optic access can provide high-speed bandwidth of 100Mbps, 200Mbps, etc.
Low loss: fiber optic media is manufactured with extremely high purity, so the loss of fiber optics is extremely low. Therefore, the number of relay stations can be reduced in the communication line, which can greatly improve the quality of communication.
Strong immunity: fiber optic is a non-metallic dielectric material, so it is not subject to electromagnetic interference.
Indoor fiber optic cables have lower tensile strength and are less protective. But they are also lighter and cheaper. This type of fiber optic is mainly used for internal wiring of buildings and interconnection of network equipment.
Outdoor fiber optic cables have an additional layer of metal armor than indoor fiber optic cables. Outdoor fiber optic cables have higher tensile strength and are mainly used for interconnection between buildings and remote networks.
ADSS fiber optic cable has no metal in its structure, so it is resistant to electromagnetic interference and lightning. It can use existing towers to build with electricity, saving line construction costs. ADSS fiber optic cable can be used in long-distance environments such as railroads and other strong electric environments, lightning-prone areas, and complex terrain.
OPGW fiber optic cable structure is fiber optic units wrapped in all metal. It can be placed in the bottom line of overhead high voltage transmission lines to form a fiber optic communication network.OPGW fiber optic cable has both functions of ground and communication, which can effectively improve the utilization rate of towers.OPGW fiber optic cable is mainly used in 500KV, 220KV, and 110KV voltage lines.
The number of cores of fiber optic cable is mainly related to the application system. It depends on how many cores of fiber are used in the specific application system, and then add the number of redundant cores in the line, you can calculate the number of fiber cores. The number of fiber cores is not related to the number of information points, but only to the number of fiber nodes.
Generally speaking, 1 to 2 cores of fiber are used for FTTH entry lines. 4 to 48 cores of fiber optic cable are generally used for operation and system integration. And backbone fiber optic cable is generally used for more than 48 cores.
Multimode fiber supports hundreds of transmission modes. This type of fiber has the advantages of high bandwidth and low cost. It is suitable for short-distance transmission (transmission distance is limited to 2000 meters).
Single-mode fiber is capable of transmitting only one mode of the signal wave. Because the optical signal only travels along a straight line in single-mode fiber, it makes the transmission band of single-mode fiber very wide. Therefore, single-mode fiber is suitable for backbone, high-capacity, and long-distance communication systems.
Single-mode fiber uses a laser or laser diode as the light source, so it costs a little more. Nowadays, single-mode fiber is widely used, while multimode fiber is gradually being phased out.
Submarine fiber optic cables need to be protected from seawater corrosion, withstand submarine pressure, and be protected from external damage, so the structure of deep-sea fiber optic cables is more complex.
The submarine optical fiber needs to be wrapped around with high-strength steel wire, and all gaps should be filled with waterproof material during the wrapping process.
Then wrap a layer of copper tape around the steel wire, so that the steel wire and copper tube form pressure and tensile resistance of the joint.
A layer of polyethylene sheathing is added to the outside of the wire and copper tube.
This tight multi-layer structure is designed to ensure the stable operation of the submarine fiber optic cable.