Underwater Cable
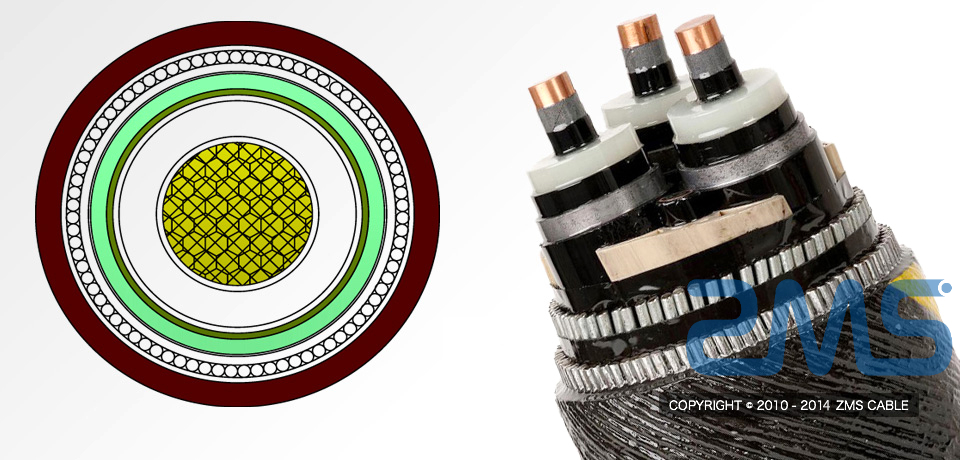
Transoceanic underwater cables are wires insulated with XLPE, PE, or EPR and covered with waterproof material, laid underwater on the seabed and in rivers for the transmission of electricity or communications.
ZMS manufactures submarine power cables in diameters ranging from 70 mm to 210 mm in both HVAC and HVDC versions, utilizing state-of-the-art cable design, manufacturing, and installation methods.
Class: HVDC, HVAC, Medium Voltage, High Voltage
Product Description
Single Core MV Submarine Cable
Medium voltage submarine cables have passed ISO9001, OHSAS18001, ISO 14001 system certification, and we can issue test reports according to IEC, ICEA, CIGRE and other standards.
Conductor: Copper wire can be tinned
Conductor shield: Extruded layer of semi-conductive material
Insulation: XLPE, PE or EPR
Insulation shield: extruded layer of semi-conductive material
Metal shielding: copper tape
Waterproofing layer Semi-conductive waterproof strip
Armouring: Seawater resistant alloy galvanized steel wire and bitumen
Standards: IEC 60228, IEC 60502, IEC 60502 IEC 60228, IEC 60502, IEC 60840, IEC 62067
Three Cores HV Undersea Cable
High-voltage submarine cables are used to transmit power to coastal islands, oil platforms, or across rivers and lakes. The cable design is based on national or international standards. Such as VDE, IEC, etc.
Conductor: Copper single wire, tin galvanized or non-tin galvanized
Conductor Shield: Extruded layer of semi-conductive material
Insulation: XLPE or EPR
Metal shield: Copper tape (lead jacket)
Waterproof sheath: composite waterproof layer (copper or aluminum tape, laminated with pe) or lead sheath (extruded lead tape laminated with PE)
Number of cores: up to 144
Lap inner layer: mesh fabric and bitumen
Armouring Armouring: seawater-resistant alloy galvanized steel wire and bitumen
Standards: IEC 60228, IEC 60502, IEC 60840, IEC 62067.
HVDC & HVAC
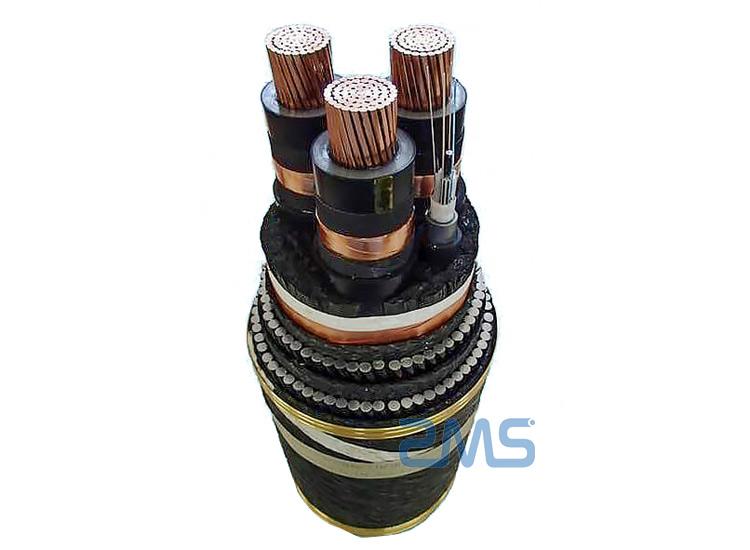
HVDC Submarine Cable
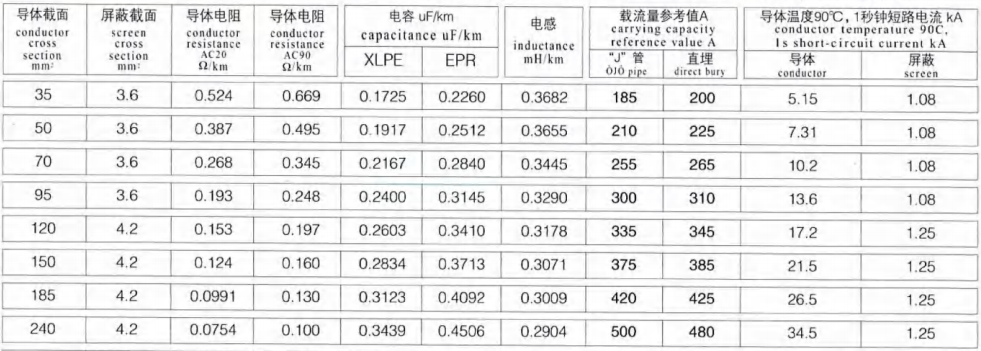
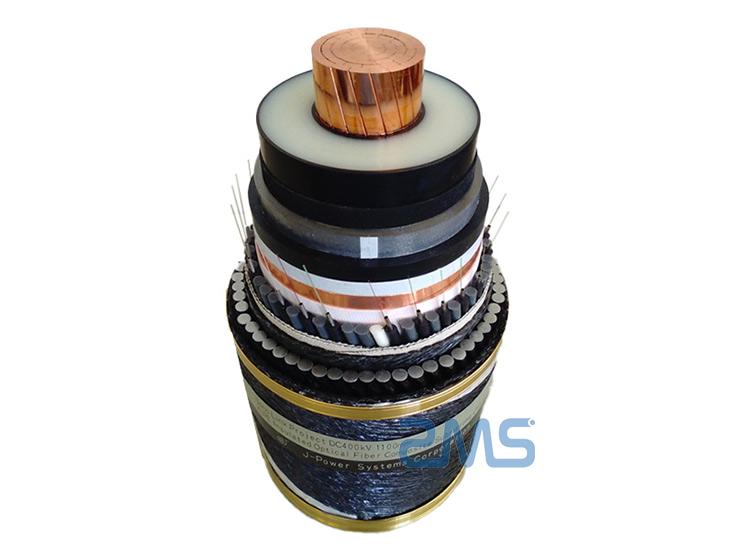
HVAC Submarine Cable
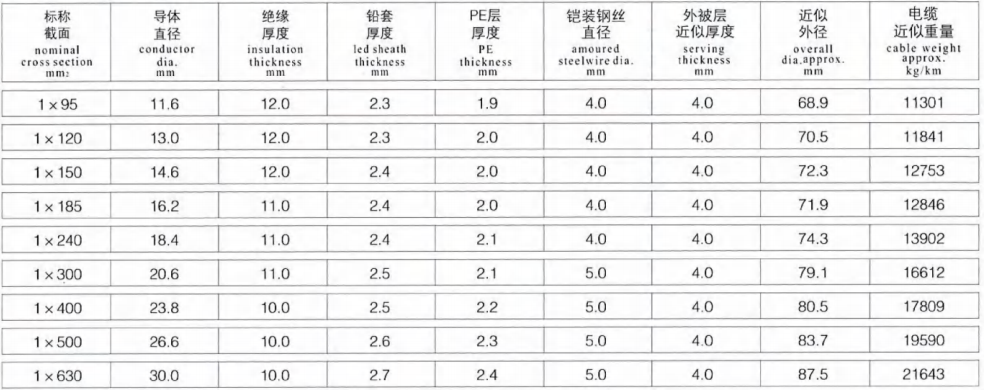
ZMS Production Advantages
ZMS produces submarine power cables in strict accordance with national or international standards, and today, HVDC cable technology is perfect for interconnecting power grids between countries or continents to ensure reliable energy infrastructure and trading.
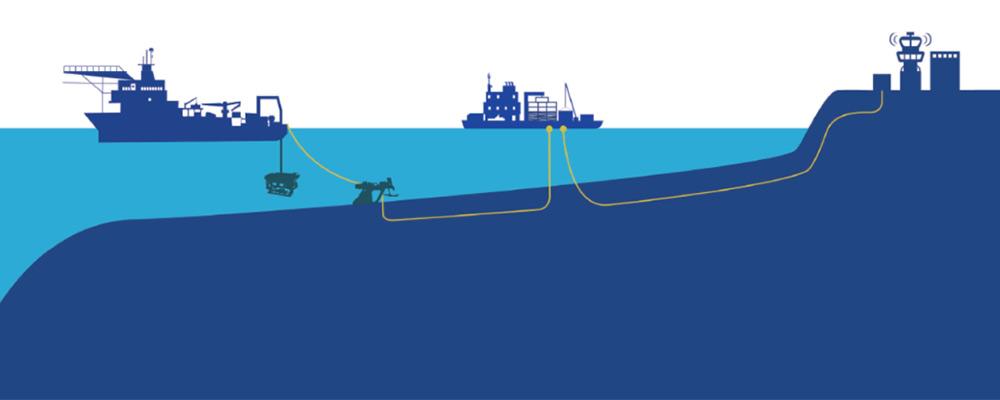
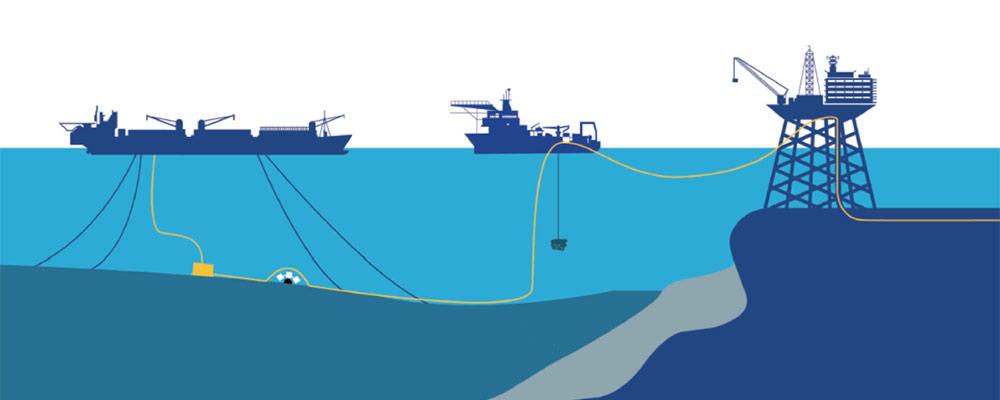
Rigorous Waterproof Construction
The longitudinal and transverse waterproofing measures set up during the production of ZMS submarine cables are a great advantage for you to choose, because when the cables are laid in water and corroded by hydrochloric acid or struck by huge objects, water stains and mist vapor will penetrate along the cracks to the inside of the cables, and waterproofing measures are perfect to avoid this hazard.
We also add a metal waterproof layer, the metal sheath, on top of the metal shielding of the submarine cable. In contrast, high-voltage underwater power cables use a metal sheath made of lead, aluminum and stainless steel. There is also the application of water-absorbent and water-blocking powders, all of which are stringent measures to ensure that no water enters the interior of the cable.
Project Installation Guidance
ZMS has worked on underwater cable projects in more than a decade in countries around the world, including Mongolia, Indonesia and Thailand. Due to the long length of submarine cables, there are always technical and methodological problems encountered when laying submarine cables, and ZMS, as a leading submarine cable supplier, is always willing to work with our customers to solve installation and technical problems once the cables are received.
ZMS Submarine Cable Manufacturing Process
The entire manufacturing process of the submarine power cable is the same as the general power cable. The entire manufacturing process of the undersea cable is the same as the general power cable. However, there are special requirements for the mechanical strength and corrosion resistance of the sea cable. And the length of the undersea cable is required to be extended as much as possible.
The following is a brief description of the manufacturing process of impregnated paper cables and extruded insulated submarine cables. Impregnated paper cable is first wrapped with an insulating paper core, followed by vacuum drying, and oil dipping, after completing the conductor core, and then wrapped with lead sheath, which is subject to the process of continuous extrusion.
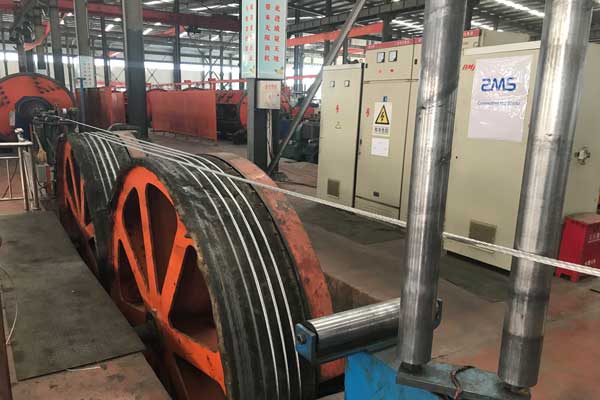
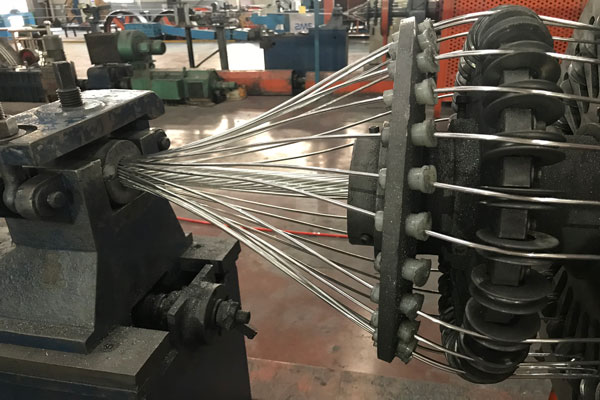
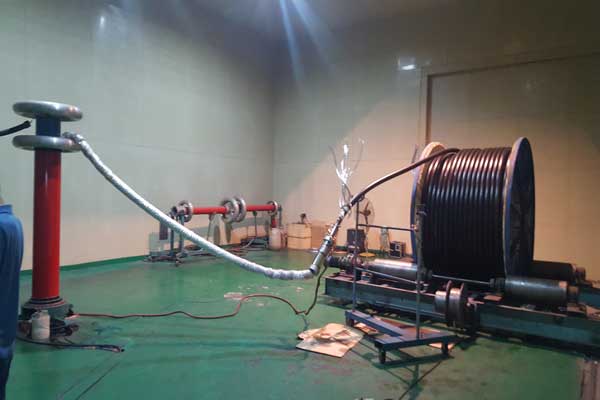
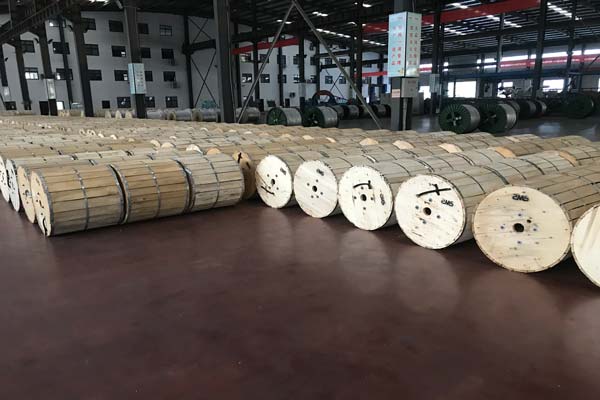
Extrusion of extremely long cable cores is an extremely important step and must be carried out night and day. The conductor core of the oil-filled cable passes through a siphon transport tube from the storage cylinder to the lead press. The tube is filled with degassing oil, which flows in the opposite direction to the conductor core to isolate the contact between the core and the air.
After the core is covered with lead, it is coiled on a rotating platform (if the cable is oil-filled or inflatable, the appropriate amount of metal reinforcement can be added). Then the underwater cable is covered with a polyethylene sheath (extruded polyethylene sheath is also a continuous operation). And then wrapped with two layers of galvanized steel wire armor, covered with oiled hemp impregnation. In the subsequent production process, the lead sheath and metal strip must be grounded through the polyethylene sheath at the appropriate stage.
Most of the production processes for cross-linked polyethylene cables and ethylene-propylene rubber insulated submarine cables are similar to those for paper-insulated lead-sheathed cables, except for the extrusion and vulcanization of the synthetic rubber insulation. But without the use of a lead sheath.
Our Quality Services
Quality Certification Services
ZMS cable products are manufactured according to GB, IEC, BS, NFC, ASTM, DIN, and other international standards. Our technical team can customize cable products that meet your requirements according to your needs.
Profession Customer Service
ZMS provides free professional consulting services to provide you with one-stop project solution services and rapid product delivery solutions.
Delivery And Shipping Services
While we at ZMS provide high-quality cables, we also provide good delivery solutions. While ensuring the safe delivery of products, we provide the best packaging and transportation solutions, greatly reducing customers’ transportation costs.
