Many people have heard of nickel metal and may not have seen it, but it is found everywhere in life. For example, the copper nickel-plated cables that we all come into contact with daily. Recently, there was this report about nickel.
Brazilian mining company Vale said Wednesday that global demand for nickel will grow 44 percent by 2030 over this year’s forecast due to strong demand for electric vehicle batteries.
In a statement, the company said it expects demand for nickel to increase rapidly this decade as the energy transition takes hold. And it added that the new forecast demand will reach 6.2 million tons.
The company also estimated that its medium-term nickel production should reach 230,000 to 245,000 tons per year, compared to the projected 190,000 tons in 2022.
The growth in nickel supply should be driven mainly by Indonesia and Canada, where the company has local operations, and Australia.
Global demand for copper – also used in automotive batteries and renewable energy systems – is also expected to grow by about 20% to 37 million tons by 2030, Vale added.
Medium-term forecasts for copper range from 390,000 to 420,000 tons per year, while forecasts for 2022 are as high as 285,000 tons. The company also expects a structural shortage of copper in the medium to long term, with increasing demand combined with a lack of supply being the main factor.
So how important is nickel metal? And what decisive role does it play in power cables? Let ZMS Cable Group take you to understand it.
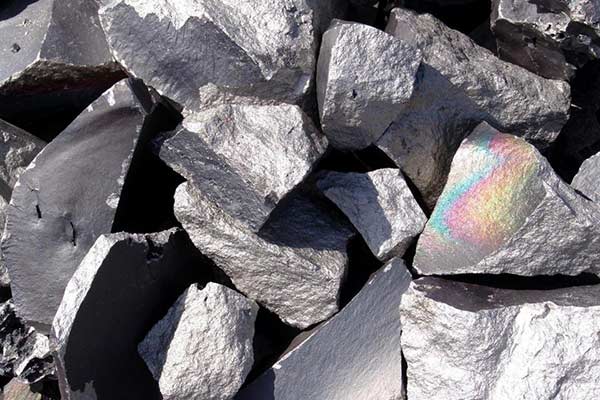
Nickel Metal Definition
Nickel, a transition metal element.
Nickel is a silver-white metal, with good mechanical strength and ductility.
Insoluble in water, very resistant to acids and alkalis, but easily soluble in dilute nitric acid and aqua regia. It is resistant to high temperatures, with a melting point of 1455 °C and a boiling point of 2730 °C. The density is 8.902 g/cm³.
It can be used to make currency, etc. Plating on other metals can prevent rusting.
Nickel Distribution
The world’s nickel resources are very rich, and the content in the earth’s crust is quite a lot.
However, it is much less than oxygen, silicon, aluminum, iron, and magnesium.
The highest nickel content in the earth’s core of the global nickel ore reserves in 2014 is the natural nickel-iron alloy.
Nickel ore is 0.018% in the earth’s crust, and ferromagnesian rocks in the crust contain more nickel than silica-aluminous rocks.
For example, peridotite contains 1000 times more nickel than granite, and gabbro contains 80 times more nickel than granite.
In the distribution of nickel resources in the world, laterite nickel accounts for about 55%, sulfide-type nickel accounts for 28%, and nickel in seafloor ferromanganese nodules accounts for 17%.
Seabed ferromanganese nodules have not been practically exploited due to factors such as mining technology and pollution of the ocean.
Nickel Physical Properties
Nickel is a silvery-white metal with good mechanical strength and ductility. It also has good malleability and corrosion resistance.
Nearly silvery-white, nickel is a hard, ductile, and ferromagnetic metallic element.
It is highly polished and resistant to corrosion. When dissolved in nitric acid, it is green in color.
It is mainly used in alloys and as a catalyst.
Nickel Chemical Properties
Nickel metal is in group VIII of the fourth cycle. It is chemically active but more stable than iron.
It is difficult to oxidize in air at room temperature and does not react easily with concentrated nitric acid.
Fine nickel wire is combustible, reacts with halogens when heated, and dissolves slowly in dilute acids. Can absorb a considerable amount of hydrogen gas.
Nickel is insoluble in water and forms a dense oxide film on the surface in moist air at room temperature, which prevents the continued oxidation of the native metal.
In dilute acids can be slowly dissolved, releasing hydrogen gas and producing green positive divalent nickel ions Ni resistant to strong bases.
Nickel can be burned in pure oxygen, emitting a dazzling white light.
Likewise, nickel can burn in chlorine and fluorine gas.
It does not react to oxidizer solutions, including nitric acid.
Nickel is also a moderately strong reducing agent.
Nickel Poisoning Prevention
1. Occupationally exposed persons to nickel should have regular physical examinations at a hospital.
Non-occupational exposure to nickel personnel should be away from areas with high nickel dust.
2. Daily stainless steel items should not hold strong acid or strong alkaline food for a long time to prevent nickel leaching.
Avoid using stainless steel utensils to decoct Chinese medicine. To prevent the alkaloids in Chinese medicine, organic acids and other reactions with it under heating conditions, etc.
3. Try not to smoke.
4. Some porcelain water cups and utensils should be carefully chosen.
5. Legislated recycling of used batteries to avoid environmental pollution.

Nickel Applications
Nickel has very good plasticity, corrosion resistance, and magnetic properties.
Therefore, it is mainly used in steel, nickel-based alloys, electroplating, and batteries. It is widely used in various military manufacturing industries such as aircraft, radar, civil machinery manufacturing, and electroplating industry.
1. Electroplating Field
Nickel plating is a durable, corrosion-resistant coating on steel and other metal substrates.
Its corrosion resistance is 20% to 25% higher than that of galvanized layers.
Nickel-plated items are beautiful, clean, and resistant to rusting.
The processing volume of electroplated nickel is second only to electroplated zinc, and its consumption accounts for about 10% of total nickel production.
Electroplated Nickel Features
1.1 High Stability
The crystals are extremely fine and have excellent polishing properties.
1.2 High Hardness of the Plated Layer
This can improve the wear resistance of the product surface.
Widely used in optical instrument plating, protective decorative plating, casting crystallizer electronic components, etc.
2. Electroless Nickel Plating
Chemical nickel plating thickness uniformity, no hydrogen seepage, no hydrogen embrittlement, and no need to remove hydrogen after chemical nickel plating.
Many chemical nickel plating products have better corrosion resistance and high-temperature oxidation resistance than an electroplated nickel.
It can be deposited on the surface of various materials without the DC motor or control equipment required for general plating.
Low heat treatment temperature can be obtained with different corrosion resistance and wear resistance after different holding times as long as it is below 400℃.
Therefore, it is especially suitable for the functional plating of parts with complex shapes and surfaces requiring wear and corrosion resistance, etc.
Copper Nickel Plated Cable
After understanding nickel, here we have to focus on the important use of nickel in the cable.
First, let’s start with the most basic cable.
A typical high-temperature cable consists of four basic parts: conductor, insulation, shield, and jacket.
Each structure does not necessarily contain all parts, and a simple structure may only require a conductor and insulation.
Usually, insulation without a protective layer is the one with better electrical insulation properties. For example, non-conductive) rigid plastic or synthetic rubber, if there are more applications at high temperatures, more complex structures are required.
Nickel-Plated Copper Cable Applications
In wire and cable design, conductor selection is based on the environment and characteristics of the wire and cable application.
The key parameters consist of conductor material, conductor diameter, and stranding.
Since conductor materials differ in terms of thermal resistance, the service temperature is considered first.
In the absence of good temperature characteristics of the conductor and insulation, the material and the conductor round mil area are the key performance determinants.
This is because it determines the current carrying capacity of the conductor.
Finally how flexible the wire and cable need to be to determine the stranded construction.
The reason for choosing nickel-plated copper cable is mainly based on the fact that copper wire of this material has better high and low-temperature strength, higher oxidation resistance, and corrosion resistance.
The shielding layer is further divided into metallic and non-metallic shielding.
The role of wire shielding is to improve the electromagnetic field distribution on the surface of the wire, used to prevent interference from its internal and external electric and magnetic fields.
It also plays a certain loop role.
The choice of shielding material is similar to that of the conductor, and its use environment and characteristics should also be considered.
The shielding material is also chosen from nickel-plated copper cables because of its better high and low-temperature strength. There is also higher oxidation resistance and corrosion resistance.
Nickel-Plated Copper Cable Plating
According to the ASTMB355 standard, the thickness of the nickel layer is classified according to the percentage of nickel content and by conductor diameter, respectively. The following standards are available for various nickel thicknesses
There are five classes of nickel-plated copper cables for wire and cable applications.
Each grade of nickel-plated copper cable is used in different applications.
1. Grade 2 a nickel content of at least 2% of the weight of the nickel-plated copper cable.
2. Grade 4 Nickel content is at least 4% of the weight of the nickel-plated copper cable.
3. Grade 7 nickel content is at least 7% of the weight of nickel-plated copper cables.
4. Grade 10 nickel content is at least 10% of the weight of the nickel-plated copper cable.
5. Grade 27 has a nickel content of at least 27% of the weight of the nickel-plated copper cable.
In addition to the above requirements for nickel content.
Nickel-plated copper cables in the core also need to consider the following conductor characteristics.
1. continuity
2. Plating continuity
3. DC resistance
4. Tensile strength and elongation at break
Because conductor continuity is the basic guarantee of the cable’s ability to transmit current.
Plating continuity is to assess the denseness of the plating on the surface of nickel-plated copper cable cores.
DC resistance is a reflection of the quality of the nickel-plated copper cable core material.
Tensile strength and elongation at break are the mechanical properties that reflect the nickel-plated copper cable core of wire and cable.
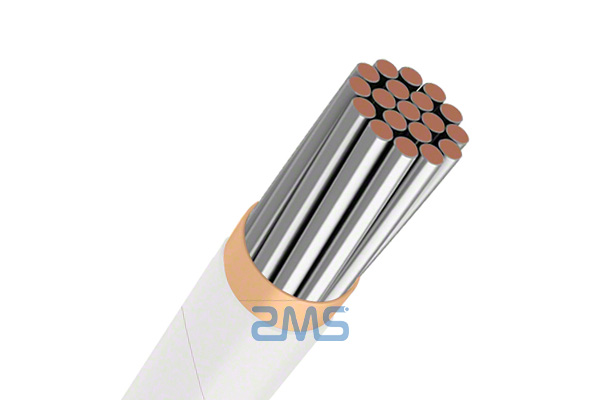
Example of Nickel-Plated Copper Cable
1. In High-Temperature Situations
All basic requirements must be considered when selecting materials for wire and cable at high temperatures.
These include current carrying capacity, voltage value, insulation material, dielectric strength, and external temperature.
The next consideration is the temperature resistance level of the insulation material allowed by the application environment. The most important of these is the thermal resistance. Many insulation sheaths and metal shielding materials, used alone or combined into a composite material, are available for high-temperature wire and cable.
Insulation, sheathing, and shielding provide excellent electrical and mechanical properties for high-temperature cables.
The first layer of insulation must have good electrical insulation to contain and direct the voltage. The second layer of insulation, if present, is used to protect the first layer of insulation and conductors from physical damage.
The outer woven shield and sheath provide additional mechanical protection for the insulation, while the sheath also serves to protect the environment.
Finally, metal armor, if present, is used to provide heavy-duty natural protection against electrically induced disturbances in harsh environments.
These disturbances occur through the engine ignition and shutdown, the stabilization and switching process when the fluorescent tube is turned on.
2. When There is Fire
Aircraft wire and cable for ignition areas. The nickel layer thickness of 10% to 27%.
Some of the FAA requirements design flammability to FAR25.
All wire insulation must meet FAR25.1359(d) for flammability. These wires and cables must also meet FAR25.1359b) in the ignition zone.
The fire-resistant electrical network wires in the engine center and engine compartment can operate at temperatures up to 350°C.
The construction is as follows
1. Nickel-plated copper cable stranded conductors
2. Glass fiber or mica-coated insulation
Other Applications
High temperature leads to iron, steel, lead, glass, and petrochemical plants.
Wire and cable with a nickel plating of 27% can be used in severe high-temperature environments.
The structure is as follows
1. Flexible
Stranded conductor of 27% nickel-plated copper cable
2. Wound tempered mica insulation
3. Tightly braided glass wire braid conductor sheath, high-temperature abrasion, and temperature-resistant color marking coating
4. Tempered flame retardant mica tape
5. Moisture-resistant and flow-resistant heat tape
6. Glass wire braid sheath with a high-temperature coating that can work in an adverse environment.
Motor lead and device cable.
Flexible stranded 2% nickel-plated copper conductor wire and cable with three layers of insulation
1. PTFE tape insulation
2. Auxiliary glass wire insulation
3. Braided fiber sheath with high temperature-resistant coating.
Continuous operating temperature 250°C, voltage 600V.
In summary, nickel-plated copper cable cores are used as wire and cable conductors in a wide range of applications with better characteristics than silver-plated and tin-plated copper cores. Therefore, we should take into account the requirements of each field of wire and cable product characteristics and the environment used in the daily design of wire and cable, to select the appropriate raw materials for design to improve the quality of each field of platform reliability and reduce the risk of wire and cable in the operation of the platform.
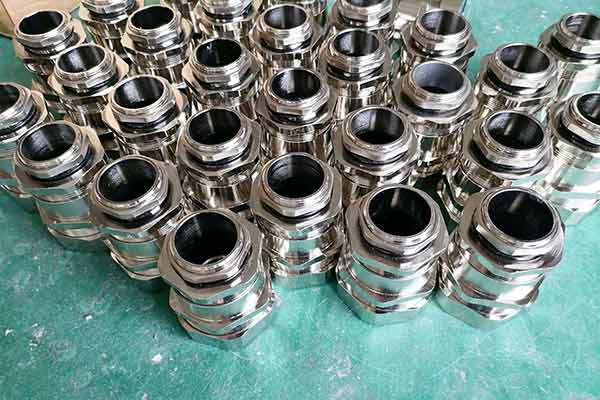
Copper Nickel-Plated Cable Glands
Performance characteristics and differences between brass nickel plating and chrome plating of cable glands.
Chrome plating layer without bottom layer polished and can be used directly.
1. Plating layer thickness
2. Plating thickness of 12~50μm is used for the plunger of the hydraulic device to improve its sealing and sex.
3. For unimportant mating surfaces, the plating thickness can be >50μm.
After plating, grinding to achieve the required dimensional accuracy to compensate for the amount of wear.
In addition to the conventional chrome plating layer, it can also be made into a loose hole chrome plating layer.
The method is to finish the hard chrome layer and then corrode it. For example, adding hydrochloric acid for corrosion.
The micro-cracks on the surface of the plated layer are widened to a surface covered with micro cracks.
This can effectively store the lubricating medium to improve the lubrication condition.
It can be used in the repair of plain-bearing journals.
A nickel plating layer can improve the surface performance of new parts, such as sliding friction vice surface nickel plating layer can be anti-scuffing.
Another example is paper, leather, and other enterprises with roll surface nickel plating layer with corrosion resistance, and resistance to thermal oxidation properties.
The plating layer thickness of 30 to 250μm, sometimes can be processed without.
For processing errors or wear the size of the larger parts. For example, compressor piston rod, hydraulic machine cylinder, piston, etc., can be used as size compensation.
Electrical plug application nickel plating treatment is also more common, the actual use of good results.
The above is the introduction of nickel and the detailed application in the cable. The world is big and there are millions of metal elements that will be waiting to be developed to facilitate people’s life. The use of nickel in cables is beneficial and not harmful for both cables and nickel.
As the world grows extremely fast, it is increasingly used for copper-plated nickel cables. And a variety of resources that can be used sustainably are being developed.
ZMS cable company has always been concerned about the development of the cable, always adheres to providing high-quality cable, good value for money, thoughtful service, the product after a strict manual qualification audit, trustworthy.
—ZMS Cable Team