AAAC Conductor
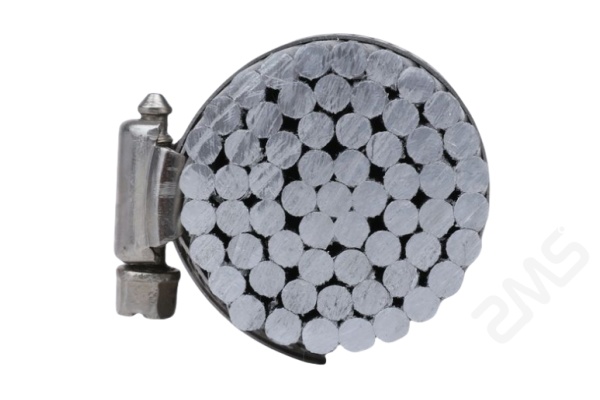
AAAC All-Aluminum Alloy Conductor is a high-strength alloy conductor consisting of concentrically stranded aluminum alloy wires, usually made of 6201-T81 material. Compared with traditional AAC conductors, AAAC conductors have superior mechanical strength and stronger corrosion resistance, making them very suitable for long-span overhead lines and installations in coastal or industrial environments.
As a professional AAAC cable supplier, ZMS produces and exports a full range of AAAC conductors that comply with IEC 61089 and ASTM B399 standards. They are widely used in utility distribution networks, rural electrification, and medium and high voltage transmission projects.
AAAC Conductor Structure
What is an AAAC conductor?
An all-aluminum alloy conductor (AAAC) is composed of multiple strands of high-strength aluminum alloy wires twisted concentrically to form a single, uniform conductor. This provides an excellent balance between conductivity and mechanical properties, making it an ideal solution for overhead transmission and distribution systems, especially for corrosive or long-span environments.
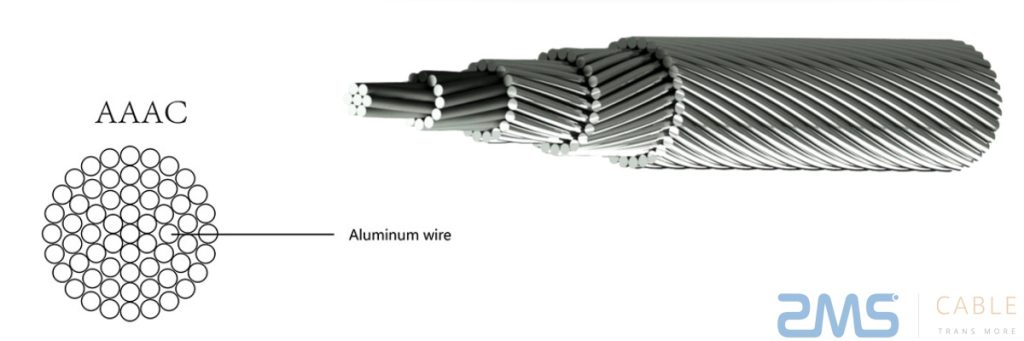
Key Structural Features Include:
- Material: Made of 6201-T81 aluminum alloy, it has higher tensile strength and corrosion resistance than standard aluminum (1350-H19).
- Stranded Wire Structure: It can be customized according to the conductor size required by the customer, using concentric twisting, with 7, 19, 37 or more stranded wire cores.
- Single Material Structure: Unlike aluminum steel core stranded wire (ACSR), AAAC does not contain a steel core, which reduces weight and improves corrosion resistance.
- Appearance: Smooth surface and uniform diameter. Ensures stable electrical contact and easy installation in overhead line fittings.
- Standards Compliance: Designed to IEC 61089, ASTM B399 and BS EN 50182.
About AAAC Strand Number
The number of strands in AAAC bare overhead conductor plays a vital role in determining the conductor’s mechanical flexibility, tensile strength, overall diameter, and current-carrying performance.
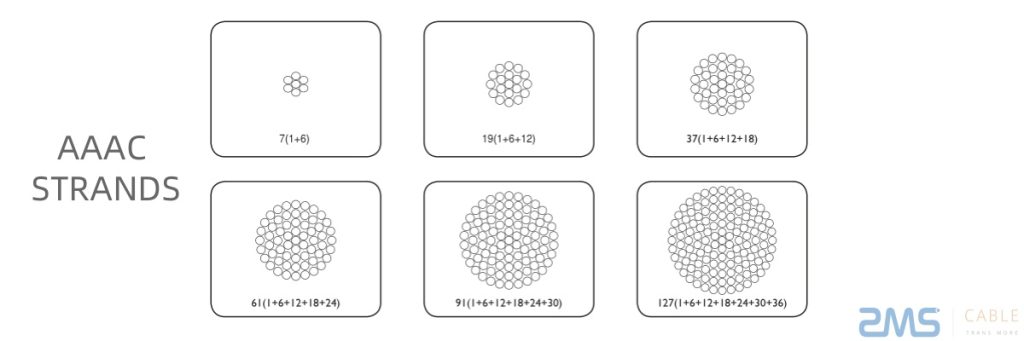
AAAC Conductor Size Chart
Stranding Type | Typical No. of Wires | Typical Application Range | Structural Characteristics | Advantages |
---|---|---|---|---|
7-strand | 7 (1 center + 6 outer) | Small sizes (up to ~70 mm²) | Compact, fewer layers | Cost-effective, easy to manufacture |
19-strand | 1 + 6 + 12 | Medium sizes (~70–200 mm²) | 2-layer structure, balanced | Good strength and moderate flexibility |
37-strand | 1 + 6 + 12 + 18 | Large sizes (~200–400 mm²) | 3-layer structure, smoother surface | Increased flexibility, better vibration resistance |
61-strand | 1 + 6 + 12 + 18 + 24 | Extra-large sizes (>400 mm²) | Multi-layer, uniform stress distribution | Excellent flexibility, ideal for long spans |
Selecting the appropriate AAAC conductor layup is critical to meeting the line’s mechanical requirements, environmental conditions, and installation practices. Whether it’s a 7-wire compact design for a simple line or a 61-wire high-flex conductor for a long span, ZMS Cable offers fully customized AAAC solutions that meet IEC 61089 and ASTM B399 standards.
AAAC Conductor Features
- Superior corrosion resistance over AAC & ACSR
- Higher tensile strength than AAC
- Lightweight and easy to handle
- Suitable for coastal, desert, and industrial environments
- Longer span capability than AAC
- Compliant with IEC 61089, ASTM B399, BS EN 50182
- Customized stranding and drum lengths available
AAAC Conductor Technical Specifications
Conductor | Stranding (No./Dia mm) | Cross-Section (mm²) | DC Resistance (Ω/km) | Rated Strength (kN) | Diameter (mm) | Weight (kg/km) | Conductivity (%IACS) |
AAAC 34.4 | 7 / 2.10 | 25.0 | 1.19 | 8.2 | 6.3 | 69 | 52.5% |
AAAC 69.4 | 7 / 3.15 | 54.6 | 0.532 | 17.8 | 9.5 | 151 | 52.5% |
AAAC 112 | 19 / 2.61 | 101.4 | 0.287 | 33.7 | 13.1 | 284 | 52.5% |
AAAC 159 | 19 / 3.10 | 144.4 | 0.211 | 47.5 | 15.5 | 398 | 52.5% |
AAAC 250 | 37 / 3.10 | 279.3 | 0.110 | 88.4 | 21.7 | 763 | 52.5% |
AAAC 336.4 | 37 / 3.45 | 336.4 | 0.091 | 106.6 | 24.2 | 916 | 52.5% |
Conductivity values are based on 52.5% IACS as per ASTM B399 and IEC 61089 specifications for 6201-T81 aluminum alloy material.
AAAC Conductor Applications
The bare conductor cable AAAC produced by ZMS has been carefully designed by the factory’s technical team, combining high strength, excellent conductivity, and excellent corrosion resistance. These characteristics make it particularly suitable for overhead power line applications in various environmental and geographical conditions.
Typical Application Areas Include:
Coastal and Industrial Environments
The corrosion resistance of the aluminum alloy in AAAC wire makes it ideal for applications in areas with high humidity, high salt air, or industrial pollutants. It outperforms conventional AAC and ACSR conductors in terms of chemical and atmospheric corrosion resistance.
Long-Span Transmission Lines
AAAC conductors have a higher tensile strength than AAC, making them ideal for long-distance and long-span installations in remote areas, such as transmission lines across valleys, rivers, or mountain infrastructure, where sag control is critical.
Urban and Suburban Distribution Networks
AAAC Bare Aluminum Conductor can also be used in medium-voltage overhead distribution systems in urban or suburban power grids, such as AAAC under the IEC 61089 standard, especially where stable performance and reduced maintenance are required.
Public Electrification and Rural Power Supply
In rural electrification projects and public facility expansions, AAAC cables provide a lightweight and cost-effective solution that combines durability and a long service life, even in remote areas.
Replacement of AAC and ACSR
AAAC conductors are often selected as direct replacements for AAC or ACSR conductors when enhanced strength or corrosion resistance is required, especially in overhead network reconstruction or upgrades.
AAAC Conductor Standards & Certificates
- ASTM B399
- IEC 61089
- BS EN 50182
- ISO 9001 / SGS / Type Test Reports available
ZMS Packing & Delivery
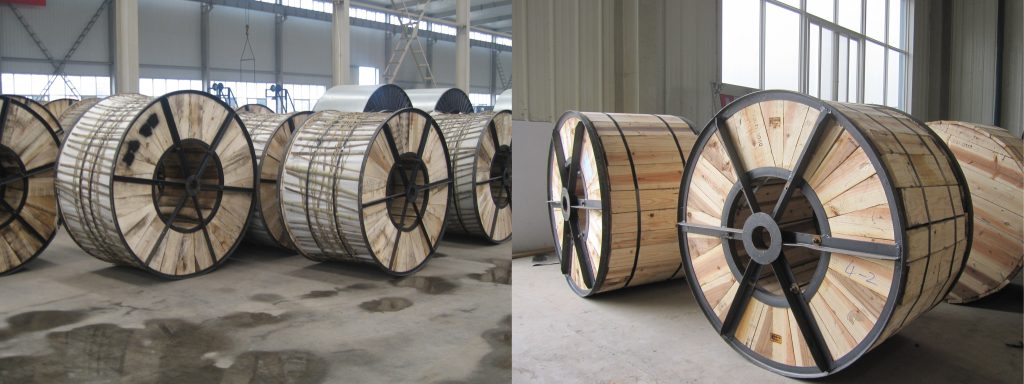
ZMS Cable packaging is provided in the form of wooden reels, corrugated boxes, and coils. The cable ends are sealed with BOPP self-adhesive tape and a non-hygroscopic sealing cap to protect the cable ends from moisture. We can print the required marks on the outside of the barrel with waterproof material according to customer requirements.
FAQ
What is the difference between AAAC and AAC?
What is the conductivity of AAAC?
Is AAAC Conductor suitable for coastal transmission lines?
Ready to order AAAC conductors or need a customized quote?