Conductor shielding:
According to relevant industry standards, cables with rated voltage exceeding 2KV need conductor shielding. Conductor shielding, also known as inner shielding, is used to form a smooth layer on the relatively rough surface of the stranded conductor to reduce the concentration of electric field at the insulation interface.
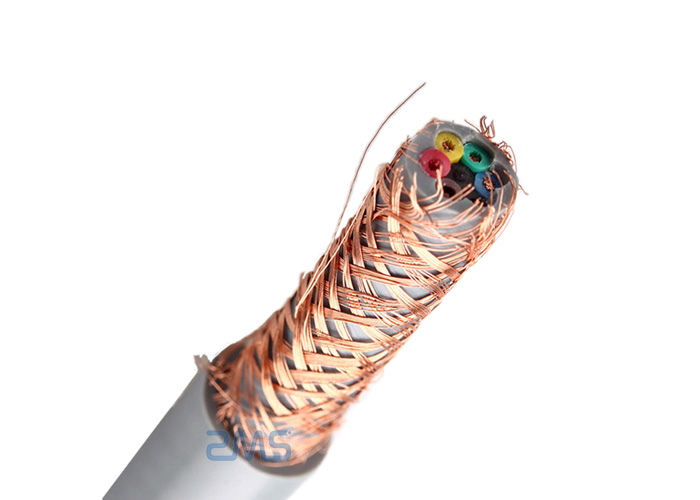
Both oil-filled cables and extruded insulation have conductor shielding. The material of conductor shielding is semiconducting material or high dielectric constant material, also known as stress control material. Both materials can reduce stress.
The conductor shielding of paper insulated cable adopts carbon black wrapping tape or metalized paper tape.
At first, the conductor shielding material spirally wrapped the semiconducting tape around the conductor. The current standard still allows wrapping tape on the conductor. This process is especially suitable for medium voltage cables with large cross-section conductors, which can tie the strand when extruding semi-conductive materials. Experience shows that it is not enough to use only semi-conductive tape. Therefore, the cable industry has changed the requirements and needs to extrude the conductor shielding layer on the conductor.
Nowadays, for extruded insulated cables, the conductor shielding layer is squeezed on the conductor as a semi-conductive layer and insulation at the same time, becoming a stress relief layer. It is very important to keep the interface between the conductor shield and insulating layer free of micropores or impurities because the electric field intensity in this area is the highest in the cable.
Today’s semi-conductive extrusion layer material is clean (minimizing impurities), and the extrusion is very smooth and round. This can greatly reduce the formation of water trees. Water trees are produced on irregular surfaces (often called protrusions) with concentrated electric fields. The conductor shielding and insulation are cross-linked at the same time during extrusion, to form a firm bond and reduce the formation of micropores at the critical interface as much as possible.
Considering compatibility, conductor shielding materials are often the same or similar to insulating materials. Special carbon black is added to the conductor shield to ensure a certain conductivity. The cable industry standard requires that the maximum resistivity of conductor shielding material shall not exceed 1000 Ω• M. These standards also require semiconducting materials to pass a long-term resistance stability test at emergency operating temperature to ensure the conductivity of the conductor shielding layer and the long-term life of the cable.
Another approach is not widely used. It is to add waterproof material to conductor shielding to realize radial moisture-proof performance. This design consists of a thin layer of aluminum or lead’s sandwich composite layer in the semiconducting material. The same composite layer design can also be used for insulation shielding.