Regarding the allowable long-term working temperature of wire and cable cores, rubber insulation is usually 65℃, PVC insulation is 70℃ and cross-linked polyethylene insulation is 90℃. The maximum allowable temperature of the conductor during a short circuit (the longest duration does not exceed 5s): is 160°C for PVC insulation and 250°C for cross-linked polyethylene insulation. ZMS cable production company to introduce the difference between XLPE cable and PVC cable.
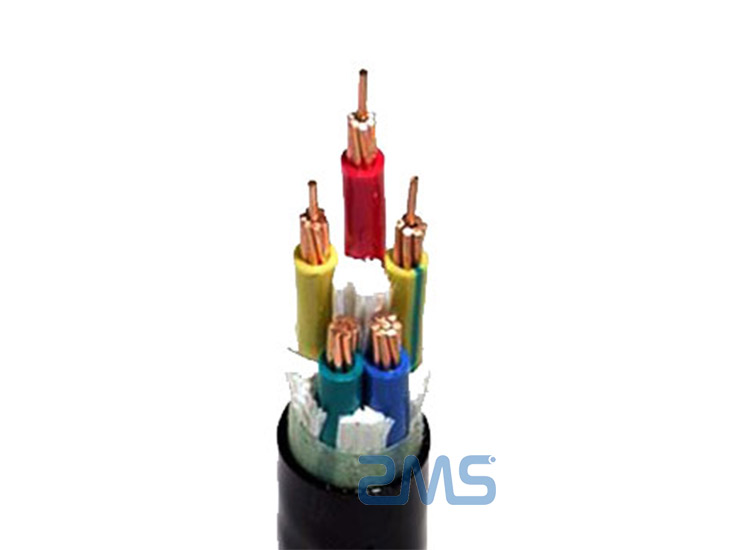
Ⅰ. The Difference Between XLPE Cable and PVC Cable
1. Low-voltage cross-linked (XLPE) cable has developed rapidly since it was put into application in the mid-1990s, and now it has half of the market share with polyvinyl chloride (PVC) cable each. Cross-linked cables compared with PVC cables, have higher load capacity, overload capacity, and longer service life (PVC cables in a better environment when the thermal life is generally 20 years, while XLPE cable thermal life is generally 40 years). The superiority of cross-linked cables is increasingly recognized by the design and use of the sector.
2. Ordinary PVC wire and cable (insulation and sheathing) burning delayed combustion quickly, fueling the fire, 1 ~ 2min that the loss of power supply capacity. Its burning decomposition of the release of black smoke can reach the level of invisible, causing breathing and evacuation difficulties. More serious is that PVC burning will decompose and release hydrogen chloride (HCL) and dioxins and other highly toxic corrosive halogen gases. This is the main cause of death in the fire (80% of the fire death factor), and diluting hydrochloric acid conductive electrical film attached to electrical equipment, seriously reduces the insulation performance of equipment, the formation of secondary disasters difficult to remove.
Ⅱ. Flame Retardant Wire and Cable
1. Flame retardant wire and cable should have flame retardant properties, according to the “bundle of wire and cable combustion test method” GB/T18380.3-2001, which can be divided into A, B, C three flame retardant grade, A-level flame retardant performance is the highest.
The U.S. Institute of Standards and Technology has conducted comparative combustion tests on flame-retardant and non-flame-retardant wires. The following test results can illustrate the importance of using flame retardant wire and cable.
a. Flame-retardant wire can provide 15 times more escape time than non-flame-retardant wire.
b. Flame retardant wire burns off only 1/2 of the material of the non-flame retardant wire.
c. The heat release rate of flame retardant wire is only 1/4 of that of non-flame retardant wire.
d. The amount of toxic gas produced by combustion is only 1/3 of that of non-flame-retardant products.
e. Smoke production performance, flame retardant products, and non-flame retardant products are not significantly different.
2 . Halogen-free low-smoke wire and cable
Halogen-free low-smoke wire and cable should have halogen-free, low-smoke, and flame-retardant performance. Its indicators are.
GB/T17650.2-1999 (halogen-free test) GB/T17651.2-1998 (low smoke test)
PH-weighted Electrical conductivity Minimum transmittance
PH ≥ 4.3 r ≤ 10us/mm T ≥ 60%
3. Fire-resistant cables
a. Fire-resistant cable burning test indicators (for fire temperature and time), “wire and cable fire resistance characteristics test method” GB12666.6-90 provides for Class A 950 ~ 1000 ℃, 90 minutes. Class B 750 ~ 800 ℃, 90 minutes. IEC331-1970 standard provides for 750 ℃, 3 hours, equivalent to our B standard. From the new draft of IEC60331, which was recently provided for voting by IEC, the supply fire temperature is still 750℃~800℃, 3 hours. If this standard is adopted, China will be equivalent to the use of fire-resistant cables will be no A, B category.
b. Fire-resistant wire and cable according to their different non-metallic materials, and can be divided into fire-retardant fire-resistant wire and cable and non-fire-retardant fire-resistant wire and cable. Refractory wire and cable domestic products to mica-covered conductors, extruded flame retardant sheath as the main body, most of the B-class products. Currently can reach the A standard with special synthetic mica tape and other mineral-insulated (copper core copper jacket, magnesium oxide insulation, also known as MI) fire-resistant cables.
Mineral-insulated fire-resistant cables are non-combustible, smoke-free, corrosion-resistant, non-toxic and impact-resistant, spray-resistant properties, known as fire-resistant cables. Fire performance in the fire-resistant wire and cable varieties is most prominent, but the manufacturing process is more complex and more expensive, the manufacturing length is limited, the bending radius is large, and the insulation is susceptible to moisture. Cross-sectional 25mm2 and above specifications are currently only available as single-core products, which must use permanent special terminals and intermediate couplers and are more complicated to install and construct.
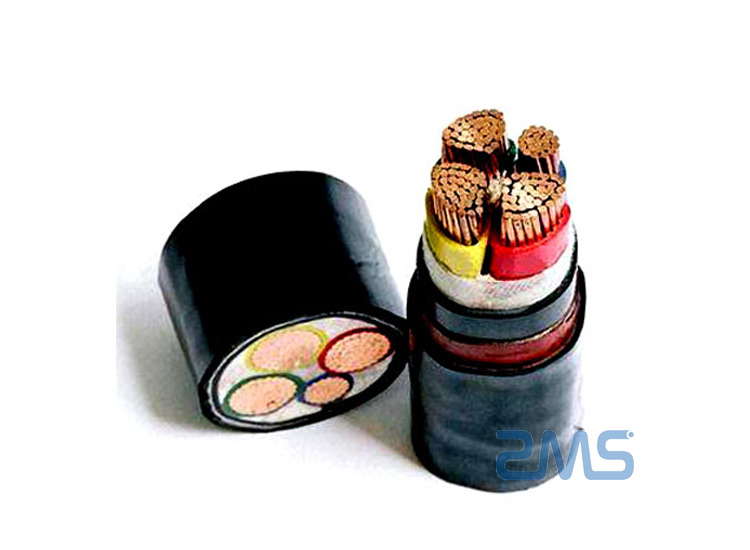
Ⅲ. The Construction of New Products with Wire and Cable
According to the “rated voltage 450/750V and below PVC insulated cable” GB5023.3-1997, 0.5 ~ 1.0mm2 wire rated voltage (insulation level) of 300/500V, 1.5 ~ 240 mm2 raised to 450/750 V.
Domestic ordinary PVC cloth wire (BV) applications still dominate but also developed new varieties of wiring suitable for construction projects:
1. Cross-linked polyolefin insulated cloth and wire (model BYJ)
As mentioned earlier, the superiority of cross-linked materials has been widely recognized, many countries have cross-linked technology applied to the field of wire, replacing PVC wire as a building wire, and has demonstrated great superiority. Some manufacturers inside and outside the province can produce cross-linked wire series and have achieved production costs and BV wire is the same. The cross-linked wire is a more ideal new building with cloth wire, Europe and the United States are vigorously promoting the application. National wire and cable industry, “15” development plan to expand the application of cross-linked wires included in the main development goals of the building with the line. Engineering applications in the province are at the initial stage.
2. Environmentally friendly cables (with flame retardant ecological materials cable, also known as EM cable)
From a technical point of view, environmentally friendly cable is a higher stage of wire and cable products, in line with the trend of the times and development trends. Upon its introduction is widely valued, Europe, the United States, Japan, and other developed countries have developed a series of product production and application standards, vigorously promoting the application.
The characteristics of environmentally friendly cables are
a. Halogen, combustion does not produce harmful gases or corrosive gases.
b. Low smoke emission when burning.
c. The same flame retardant properties as the current polyolefin cable.
d. With lead and other heavy metals, no environmental hormones, no soil pollution.
e. It can be reused.
3. Nylon-sheathed wire (model BVN)
International traditional building wiring wire is divided into two categories: a class of polyvinyl chloride wire, mainly in Europe, Japan, China, Australia, etc. Another category to the United States, and North American countries as representatives, mainly using polyvinyl chloride insulation nylon sheathed wire. It should be noted that the application of nylon sheathed wire in the United States is the development and evolution of polyvinyl chloride wire, which has a history of nearly four decades, with a market share of up to 90% in previous years.
Nylon has a soft armor, compared with polyvinyl chloride wire, superior mechanical properties, heat resistance, chemical stability, resistance to tension, and wear resistance is outstanding; compared with BYJ wire, BVN wire is usually more expensive, containing halogen, the cost performance is at a disadvantage. It should be noted that the United States is currently strongly opposed to the application of PVC, BVN applications will be significantly reduced.
4. Prefabricated branch cable
Prefabricated branch cable was developed by Japan, the mid-1990s began to introduce China. In just a few years, some domestic manufacturers have mastered and solved the relevant key technologies and manufacturing processes, and product performance and quality have reached international standards, and have been widely used in construction projects. Compared with the plug-in bus bar, the insulation, waterproof, seismic, branch reliability, and economic index of prefabricated branch cable are very outstanding. It is especially suitable for a trunked distribution system with a more stable load, and the application prospect of construction engineering is very broad.
5. Anti-rodent, anti-termites cable new varieties
Research results show that rats gnaw wire and cable not only to grind their teeth but also as part of feeding. In the southern region of humid places, cable suffers from termite damage cases gradually increased. Building engineering wire and cable anti-rodent, anti-termite hazard work should not be ignored.
IV. Summary
In conclusion, this article has introduced the advantages and disadvantages of each XLPE and PVC. You should also check the various industry standards when selecting wire and cable for your application. ZMS cable offers a wide range of XLPE cables and PVC cables at the best prices in the industry.
—ZMS Cable Group