Electric Cable Export FAQ
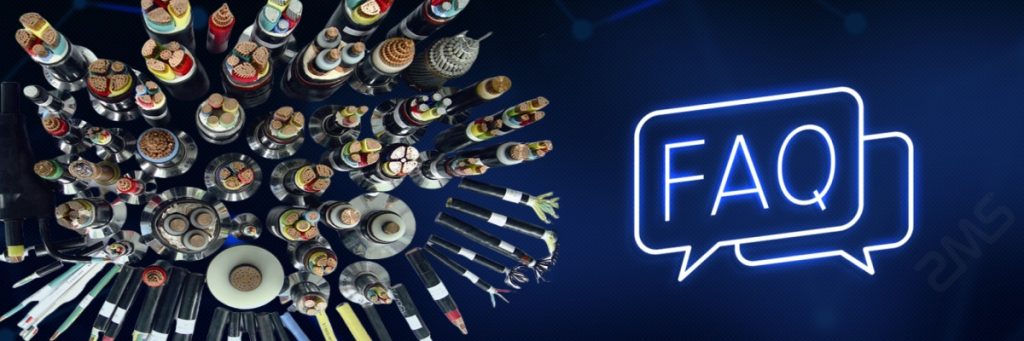
1.Which international standards do your cable products comply with?
ZMS cable products comply with various international standards, depending on the type and application required by the customer. These standards include:
- IEC (International Electrotechnical Commission) general electrical and power cable standards.
- ISO 9001 quality management system certification.
- UL (Underwriters Laboratories) safety and fire protection standards, especially for the North American market.
- CE (European Conformity Assessment Standards), in line with EU safety, health, and environmental requirements.
- RoHS (Restriction of Hazardous Substances Directive), in line with environmental safety requirements.
- EN (European Standards) and BS (British Standards) for specific cable types.
Our cables have also been involved in power projects in Spain, Mexico, and other regions. We are also familiar with Portuguese power standards and can produce cables to customer-specific requirements or project-specific standards, including customized testing protocols and third-party certification. Please get in touch with us for your specific needs.
2.What's the minimum order quantity (MOQ) ? Do you support sample order?
The minimum order quantity (MOQ) is generally 300m, but ultimately depends on the specific cable type and customization requirements, including the customer’s project size.
In addition, sample ordering of cable products may vary depending on inventory and cable type. Please contact our sales team to discuss your specific needs and we will recommend the best solution for your project.
3.What are the customizable ranges of the products? Labels? Colors?
We offer a wide range of customization options to suit your specific project or needs.
These customizable options include:
- Cable Construction: conductor size, number of cores, shield type, insulation, and jacket materials (e.g, PVC, XLPE, LSZH).
- Color Options: Insulation and jacket colors can be customized according to international color codes or customer requirements.
- Labels & Printing: company name, cable specification, batch number, meter mark, or custom text/symbols can be printed on the cable jacket.
- Packaging: wooden drum, plastic reel, roll, or custom packaging with your brand and export mark.
- Length Per Roll: The reel length can be adjusted according to installation or transportation requirements.
If your project has specific technical or visual requirements, ZMS can also provide OEM/ODM production and customized technical specifications. Just send us your drawings or technical data sheets, and we will do the rest.
4.Can you provide the cable technical parameter sheet or test report?
Yes, all our cable products are available with technical data sheets and test reports.
The technical data sheets contain detailed cable specifications, such as conductor material, insulation type, rated voltage, operating temperature, outer diameter, weight and applicable standards.The test reports can be issued by our internal quality control department or designated third-party testing agencies, depending on customer needs, covering key tests such as insulation resistance, conductor resistance, high voltage resistance, flame retardancy, etc.
These documents are usually sent together with the pro forma invoice or goods, and we can also provide them before order confirmation for project bidding or technical evaluation.
1.How to choose the appropriate cable cross-section?
The appropriate cable cross-sectional area depends on factors such as current load, voltage level, installation method, cable length, ambient temperature, and local safety standards. Selecting the right size ensures safety, minimizes voltage drop, and maximizes performance. Our technical team can assist you in making the selection based on your project needs.
2.What cables do you have for high/low temperature/corrosive environments?
ZMS Cables offers a range of special cables designed for harsh environments, including high temperature cables (up to 250°C), low temperature cables (down to -60°C), and corrosion-resistant cables made of materials such as Teflon (PTFE), silicone rubber, or halogen-free compounds.
Let us know your application and project, and we will recommend the most suitable cable type.
3.What is the service life of a cable? What factors affect it?
The typical service life of a cable is 15 to 30 years, depending on the type of cable and the application environment. Key factors affecting the service life of a cable include operating temperature, installation quality, mechanical stress, exposure to chemicals or UV rays, and overload. Proper installation and regular maintenance can significantly extend the service life of a cable.
4.What are the differences between different insulation materials (such as PVC, XLPE, PE)?
PVC is more flexible, highly flame-retardant, and economical; XLPE has higher temperature resistance and better electrical properties; PE has excellent moisture resistance and lower dielectric loss.
The specific choice depends on the installation environment, voltage leve,l and mechanical requirements, etc.
1.What large-scale engineering projects have you participated in?
We have supplied cables for various large-scale cable engineering projects in Southeast Asia, the Middle East, Africa and South America, including transmission lines, solar power plants, railway systems, oil and gas facilities and data centers. If necessary, you can contact us for detailed information on the project.
2.Can you recommend a suitable cable based on the usage environment?
Of course, our team can provide customized cable selection according to the specific environment of your project – whether it is underground, underwater, high temperature, corrosive environment, or outdoor installation, just share your application details and our technical team will recommend the most suitable cable type. Looking forward to working with you.
3.Do you provide on-site technical support or overseas services?
First of all, you need to understand that we are in different countries and regions. We guarantee to provide remote technical support for all projects. In large or strategic projects, our business personnel and technical teams can provide installation guidance, testing and troubleshooting assistance locally and internationally depending on the scope of the project. Thank you for your understanding.
1.How can I track the progress of my order?
After the order is confirmed, we will regularly provide you with the latest information on production, including production status, quality inspection and delivery information. After delivery, we will provide you with logistics information in a timely manner, and you can check it on major logistics platforms based on the information. You can also contact our sales team at any time to get real-time order tracking and support.
2.Can you provide technical information or installation guide in English?
Yes, we provide detailed cable English technical data sheets, installation manuals, and product catalogs to support your project needs. These documents can be sent before or after order confirmation, according to your requirements.
3.What are the methods of after-sales support? Phone/Email/Remote?
We provide comprehensive after-sales support via phone, email, video calls, and remote technical support. Our team is always ready to answer installation questions, troubleshooting, and any quality concerns to ensure your project goes smoothly.