The full name of the carbon fiber wire is carbon fiber composite core aluminum stranded wire (ACCC), the wire from the beginning of this century has only been used for a relatively short period of more than ten years, there is a certain amount of experience in the application. Carbon fiber wire has high strength, lightweight, high modulus of elasticity, small coefficient of linear expansion, small arc sag, small line loss, large capacity (allowing high temperature), corrosion resistance, long service life, and other characteristics. Especially suitable for coastal, mining areas corrosion intensity, high fouling strength, the wire is easy to dance the use of the environment.
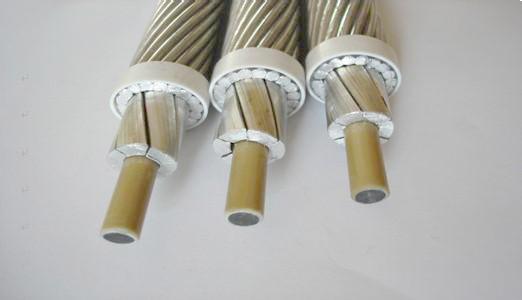
The background of the development of the wire is the original transmission line transmission capacity has been unable to meet the rapid growth of the load, replaced by a larger cross-section, a high-carrying capacity of the wire or new dedicated line is imperative. Demolition of old lines, transforming towers. And then erect new conductors of the traditional method of high cost, long construction period, or the original line channel under the difficulties of land acquisition, resulting in new lines will not be able to use the original line channel to the power grid planning and construction has brought great difficulties. That, to a certain extent, to increase the cost of the project and extend the construction cycle. Line erection process of long blackouts, but also greatly affect the reliability of the power supply and equipment available Coefficient. To solve the above contradictions, looking for a way to use the original line channel and minimize the transformation of the tower. But also can significantly improve the line transmission capacity of engineering construction methods to become the only way out, in this case, there is a carbon fiber cable.
Carbon fiber wire has many of his advantages but also has its shortcomings, such as most carbon fiber wire carbon-fiber core single core (it is understood that now in the development of carbon fiber core stranded wire), construction is easy to damage because in the aluminum stranded inside, should not be found, damaged on the future operation will leave a few security risks. Today, I collected some easy to appear in the case of the problem to share with you, mainly in the construction phase, and some notes on the operation to do a simple explanation.
Defect type 1: surface burr
Situation introduction.
In a 500kV overhead transmission line capacity transformation, the original steel-core aluminum-stranded wire to replace the carbon fiber wire. In the construction, of carbon fiber conductor wire arrival, open acceptance found that the wire surface burrs.
Cause analysis.
Manufacturers of production and processing process defects, resulting in burrs on the surface of the wire.
Consequences.
After the line is put into operation will cause corona and tip discharge phenomena.
Suggestions.
Supplies should be accepted disk by disk upon arrival.
Defect type 2: broken strands
Description of the situation.
In a 500kV overhead transmission line capacity transformation, the original steel-core aluminum-stranded wire to replace the carbon fiber wire. In the construction of the line, the wire was found to have broken strands, the broken strands were not found in the construction of force traces.
Broken strand
Cause analysis.
Manufacturers of production and processing defects, resulting in the factory wire broken strands.
Consequences.
After the line is put into operation will produce loose strands and the phenomenon of throwing strands.
Suggestions.
After the arrival of materials should be accepted disk by disk, the three-span section should focus on acceptance.
Defect type 3: “lantern”, bulging
Situation description.
In a 220kV transmission line capacity transformation project, the original 1 × LGJ-400/35 type steel-core aluminum stranded wire was replaced with 1 × JRLX/T-400 type carbon fiber wire. In the process of wire construction, the wire “lantern”, is a bulging phenomenon.
“Lantern”, bulging
Cause analysis.
Carbon fiber wire is made of the inner carbon-fiber core and outer aluminum stranded, carbon fiber wire in the exhibition or tightening process, due to the role of tension, carbon fiber wire surface aluminum wire will occur “creep elongation” (there will be a gap between the aluminum strands, the force between the wire strands against the tighter, the gap becomes smaller, although the length of the wire for a change) Although the length of the wire is changed, but the whole wire elongated), the inner layer of carbon fiber core rod due to high strength, deformation is small. The outer layer of aluminum wire and the inner layer of carbon fiber core bar will occur relative to the slip, when the slip received obstruction or a side of the endurance line clip crimping completed, will lead to carbon fiber wire surface aluminum strands appear “lantern” (bulging).
Consequences.
(1) carbon fiber wire aluminum “lantern” (bulging), for the operation of the line, generally difficult to repair, aluminum line loose also leads to long-term exposure of the carbon fiber core in the air, if the operating environment is poor, the carbon fiber core is not conducive.
(2) aluminum line “lantern” (bulging), due to changes in tension during operation, will make the surface of each layer of the aluminum line unevenly stressed, resulting in aluminum line broken strands.
Suggestions.
(1) each wire manufacturers in the processing of technical indicators are not the same, which will lead to the finished wire stranding degree of elasticity is not the same, before the operation should be the manufacturer technical briefing, in strict accordance with the manufacturer’s operating requirements exhibition tightening the wire.
(2) in the construction process of tightening the wire hanging should use special pre-stranded tensioning tools, and reduce the use of pullers and wire jammers to avoid the phenomenon of stress concentration.
(3) large tensioning section of the construction process, in the tightening of the line before painting, in the case of meeting the length of the tensioning section, should be tightened after the remaining line of the wire on the side of the tightening, so that the “creep elongation” of the aluminum line as far as possible in the open break runoff.
Defect type 4: broken wire
Description of the situation.
In a 220kV transmission line capacity transformation, the original 2 × LGJ-300/25 type steel-core aluminum stranded wire was replaced with 240/30 bifurcated carbon fiber composite core aluminum stranded wire. In the process of erection line construction breakage occurred, are used in the air crimped wire in the hanging line from the crimp zone of the tension-resistant wire clamps (near the mouth of the pipe) breakage.
Break line cause analysis.
After the relevant tests, dissecting the broken line tensioning clamps, and other ways to verify the reasons for the broken line, from the analysis of the test conclusions, there is mainly carbon fiber wire carbon core radial pressure test failed. National standard GB/T 29324-2012, the national network standard Q/GDW 1851-2012 are required to radial pressure standard for “interception length of not less than 100mm composite core bar, to 1mm / min to 21mm / min loading speed smooth loading to damage, the composite core bar should withstand not less than 30kN pressure, its end should not (cracking and peeling), but the test carbon fiber wire does not meet the requirements, the supplier of this type of wire own production of carbon fiber core can not meet the requirements of the standard, the current national standard on carbon rod radial pressure test requirements, the majority of domestic suppliers only Φ7.5 and above the specifications of carbon rod can meet, the Φ6 carbon rod radial pressure test is difficult to achieve It is difficult to meet the requirement of radial pressure test for Φ6 carbon rods with the specimen of 100mm not less than 30kN. Comprehensive relevant test conclusions and investigation, analysis of the broken line causes mainly focused on the crimping process may exist in the overpressure and other crimping process problems, as well as the quality of the wire products.
Causes the consequences.
Broken wire
Recommendation.
Carbon fiber wire in the construction process should be strictly enforced “carbon fiber composite core overhead wire construction process and acceptance guidelines (for trial implementation)” in the relevant provisions.
Defect type 5: outer scratch
Defect description.
A 500kV transmission line capacity transformation, the original LGJ-400/35 steel-core aluminum stranded wire replaced with JLRX/F2A-460/40-26 carbon fiber wire, line completion acceptance process found in the wire wear, cracks.
Outside scratch
Cause analysis.
Wires in the transport and exhibition process were cut by sharp objects led to a carbon fiber outer layer of soft aluminum scratches, and scuffs.
Consequences.
Affect the appearance of quality, but also corona, serious wire burns, and even cause broken wire accidents.
Recommendation.
After the arrival of the material should be accepted disk by disk, and the wire should be accepted file by file after the exhibition.
Defect type 6: loose strands
Defect description.
In a 500kV transmission line capacity transformation, the original LGJ-400/35 steel-core aluminum stranded wire was replaced by JLRX/F2A-460/40-26 carbon fiber wire, the line completion acceptance process found that the wire running strand.
Analysis of the reasons for loose strands.
The guide wire in the process of spreading through the pulley when the spreading angle is too small or pulley type mismatch leads to over the line by extrusion and lose shares. wire spreading completed, accessories installed when the line is too tight to twist the wire leads to losing shares.
Consequences.
Affect the appearance of quality, but also corona, serious wire burns, and even cause broken line accidents. At the same time will also affect the strength of the wire.
Suggestions.
After the arrival of the material should be accepted disk by disk, and the wire should be accepted file by file after the exhibition.
Defect type 7: wear and tear
Defect description.
A 500kV transmission line capacity transformation, the original LGJ-400/35 steel-core aluminum stranded wire replaced with JLRX/F2A-460/40-26 carbon fiber wire, line completion acceptance process found in the pre-stranded wire end of the ring-shaped wear marks.
Analysis of the reasons for wear and tear.
First, the wire pre-stranded wire tying the last few strands is not easily in place, the use of screwdrivers and other tools to pry up when scratched, the second is pre-stranded wire tying found to be in the wrong position again when removing pre-stranded wire construction protection is not in place to damage the wire.
Consequences.
Affect the quality of appearance, but also corona, serious wire burns, and even cause broken line accidents. At the same time will also affect the strength of the wire.
Suggestions.
Should focus on strengthening the acceptance of pre-stranded wire near the wire.
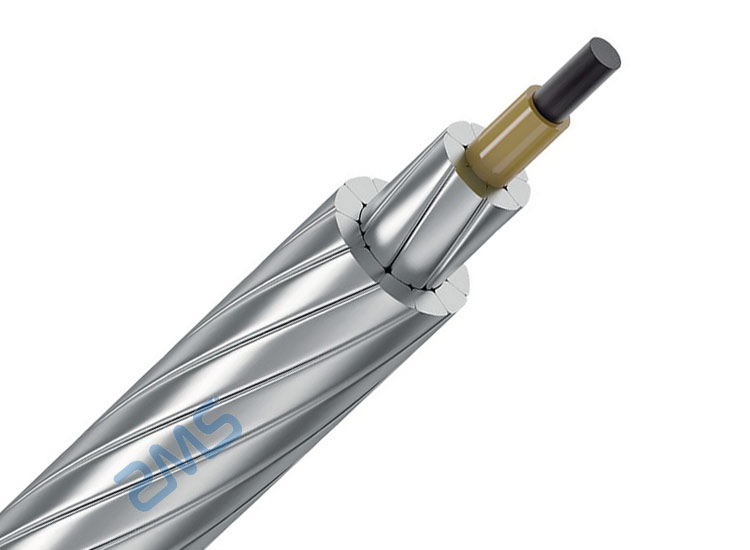
Summary
Through the above three projects 7 types of defects summary, found the following two aspects of the problem.
1. Carbon fiber quality problems, due to manufacturers not in strict accordance with the corresponding regulations and specifications processing, resulting in some of the parameters of the product failing, to the construction process and even the operation of the unpredictable hidden risks.
2. poor construction process, some construction units are still using the traditional wire construction methods, resulting in carbon fiber wire bulging, broken strands, and even broken lines.
The above two problems to the operation of certain security risks, especially the quality of the product, based on the current case, the main carbon rod does not meet the specification requirements, however, the carbon rod is the force-bearing part, the unqualified carbon rod is bound to cause a decline in the mechanical properties of the wire, even if the construction process is good, the running process encountered poor working conditions, it is also very easy to break the line accident.
As a running unit, the use of carbon fiber needs to pay attention to the following aspects of matters:
1. Because of the development of carbon fiber wire although more than a decade, but not much use in engineering, running experience is lacking, important across, large across is not recommended to use carbon fiber wire, you can choose the same current-carrying capacity of aluminum alloy core high conductivity aluminum stranded wire.
2. Strictly initial review, especially the capacity project, there must be a detailed wire selection program, the careful selection of carbon fiber wire. To determine the use of the carbon fiber wire project, understand the design unit provided by the carbon fiber wire positioning temperature and the maximum allowable temperature, understand the corresponding wire arc sag characteristics, as well as the way the wire connector selection.
3. Because of the importance across once the problem, the impact is too large, in order to important across where the tension section can be safe and reliable operation, important across in principle shall not use carbon fiber wire, can use the same current-carrying capacity of aluminum alloy core high conductivity aluminum stranded wire.
4. Strictly implement the “carbon fiber composite core overhead conductor construction process and acceptance guidelines (for trial implementation)”, to master the construction unit crimping process, spot check the quality of crimping, 500kV lines do a good job by file alignment, 220kV lines to take photos along the line and other ways, do a good job in the middle and completion of the link acceptance, good acceptance.
5. on the construction unit in the construction process and the carbon fiber wire has a hard contact, such as the location of the wire jammer stuck in the wire, etc., put forward trace record requirements to avoid problems after the occurrence of tug.
6. For the carbon fiber lines that have been put into operation, the maintenance process to try to avoid the use of flying cars out of the line to prevent the emergence of aluminum strand deformation, while properly prepared for some of the carbon fiber wire broken strands of high-temperature pre-twisted patching strips.
7. Explore practical ways to detect the core bar breakage, because the core bar is currently a single-core, from the beginning of the breakage to the broken line, there is no effective means of detection, so explore effective detection methods to master the development of carbon rod breakage law, it is imperative.
8. Advocate the whole life cycle of carbon fiber wire operation concept, from the beginning of the operation, a comprehensive grasp of the operation, assessment of the operating conditions, inferring the remaining operating time, is also an extremely critical issue, because once the carbon fiber wire into the end of life, the operating unit is equivalent to a time bomb, so it is recommended from the perspective of the whole life cycle, to master the best carbon fiber wire running time, for the follow-up Replacement to provide strong support, to avoid major failures and then replace.
Carbon fiber wire as a new wire, for capacity transformation, has a very good effect, is expected in the future industry, the old line in the capacity transformation will be used in large quantities. But due to the current lack of operational experience, for such products, the operating unit is a generally conservative attitude, because broken lines and other failures will bring enormous safety pressure on the operating unit.