NKT Receives €155 Million Submarine Cable Order
European cable manufacturer Ankett NKT has been awarded a €155 million cable order for the electrification of the North Alvheim North (NOA) and Krafla offshore fields in the NOAKA region of the North Sea.
The project includes the design, manufacture, and installation of more than 255 kilometers of 145 kV high voltage AC cable by cable-laying vessel NKT Victoria. The project includes both onshore and offshore installations and the full electrification of the fields.
Alexander Kara, President, and CEO of NKT said: “With this order, we continue our long-term partnership with Equinor to ensure the electrification of the Norwegian offshore industry. Once operational, our power cable solution will help reduce emissions from the Norwegian continental shelf.”
The project includes infield cables connecting the two main platforms, followed by a combined export cable to connect the fields to the onshore grid at the Børdalen substation in eastern Bergen, Norway.
The power cables required for the project will reportedly be manufactured in Karlskrona, Sweden, with production starting in 2024 and commissioning beginning in 2026.
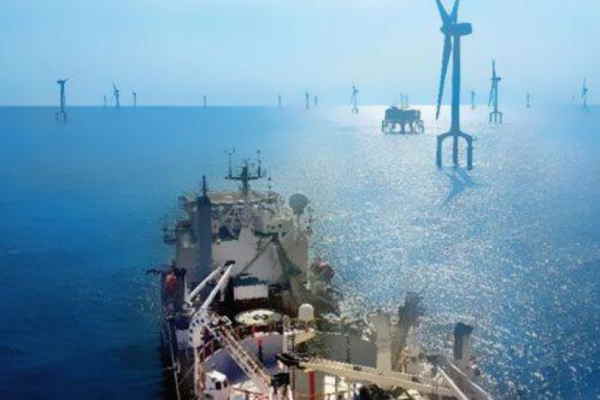
In-Depth Analysis Of Submarine Cables (AC Cable Characteristics)
In recent years, global Internet transportation methods commonly use transoceanic submarine cables instead of satellites to ensure transmission rates and save operating costs.
So how is the submarine cable made? How is the laying process? How fast is the transmission rate? How popular are they today? Here are some basic facts about submarine cables.
Materials Used To Make Them
The core of a submarine cable is made of hair-thin, high-purity optical fibers that guide light along the path of the fibers through internal reflection.
The submarine cable must be able to withstand the tremendous pressure of being 8 km underwater, equivalent to the weight of an elephant placed on a recognized thumb.
Production Process
In the making of a submarine fiber optic cable, the optical fiber is first embedded in a jelly-like compound that protects the cable from damage even in the event of contact with seawater. The fiber optic cable is then packed into a steel tube to prevent the pressure of the water from damaging it.
Next, it is wrapped in an overall very strong steel wire and snapped into a copper tube, and finally, a protective layer of polyethylene material is applied.
Near the coast of the continental shelf, submarine cables are usually laid with lightweight cables with stronger steel wires and covered with an asphalt coating to prevent corrosion by seawater.
Submarine Cable Laying
Submarine cable laying mainly includes cable routing survey and cleaning, submarine cable laying, and flush burial protection in three stages.
The cable laying should control the angle of the cable into the water and the laying tension by controlling the sailing speed of the laying vessel and the cable release speed to avoid damaging the cable due to too small a bending radius or too large a tension.
Among them, when laying in the shallow section, the cable laying vessel stops at 4.5 km from the shore and tows the cable placed on the floating package through the tractor on the shore. After the cable is put ashore, the floating package is removed and the cable is sunk to the bottom.
When laying the deep-sea section, the cable-laying vessel releases the cable and constantly monitors and adjusts it using an underwater monitor and underwater remote control vehicle to control the forward speed and direction of the laying vessel and the speed of laying the cable to avoid damaging the cable by bypassing the uneven places and rocks.
Capacity
The submarine cable can carry up to 80Tbps of data, which is equivalent to transmitting 4.7GB capacity in one second.
Development history: The world’s first submarine cable was a cable that ran across and under the English in 1851, more than ten years before Bell invented the telephone.
As early as 1995, half of all communication transmissions were made via satellite, and the development of submarine cables has gained tremendous growth compared to previous transmission methods. Hundreds of submarine cables connected the world, while satellites took a back seat and were only used to connect remote areas and certain small islands.
Pervasiveness
Ninety-nine percent of transoceanic Internet data transmission now takes place over submarine cables. There are currently 39,000 kilometers of submarine cables connecting 33 countries and four continents.
Failure History
Although sharks have been recorded by cameras damaging submarine cables once, sharks and other fish have caused less than 1% of submarine cable failures since 2006.
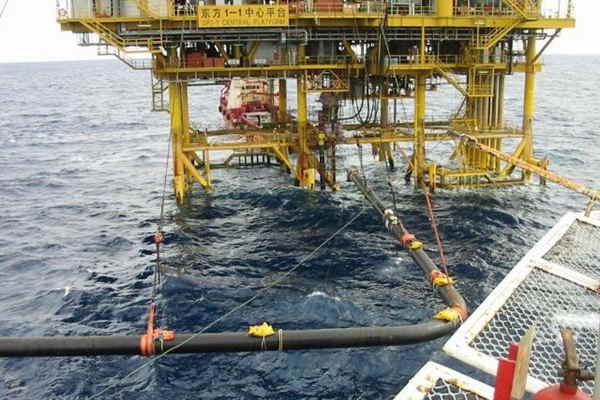
Types Of Submarine Cables
The types of submarine cables can be classified in three ways.
- The number of conductive cores. Mainly divided into three-core submarine cable and single-core submarine cable, low-voltage lines using a three-core submarine cable, and high-voltage lines using a single-core submarine cable are the majority.
- Transmission function. Traditional submarine cable is only a simple electrical energy transmission function, the new submarine cable belongs to the photoelectric composite cable, effectively realizing the electrical energy and signal transmission in the same cable.
- Load type. Divided into DC submarine cable and AC submarine cable, DC submarine cable is characterized by small losses, easy to achieve long-distance transmission. But the application of DC submarine cable experience is not rich, DC converter stations and other supporting construction costs are high, and AC submarine cable loss, but the operation and maintenance technology is mature, and supporting construction costs are small. Therefore, submarine cable line designers usually have to make technical and economic trade-offs to maximize the benefits.
Summary
Submarine cables are one of the most important pieces of equipment for submarine power transmission projects. Because submarine cable lines are long and expensive, improving operational performance, especially their transmission capacity, is one of the important objectives of submarine cable research and development. DC submarine cable in the same conductor cross-section, the same cable type, and similar laying environment conditions, its transmission capacity (power) is far more than AC submarine cable, and low operating losses and longer allowable line length.