In order to better facilitate engineers to quickly grasp some of the expertise of thermocouples. I have collected the thermocouple 15 difficult questions about thermocouples, the details are as follows.
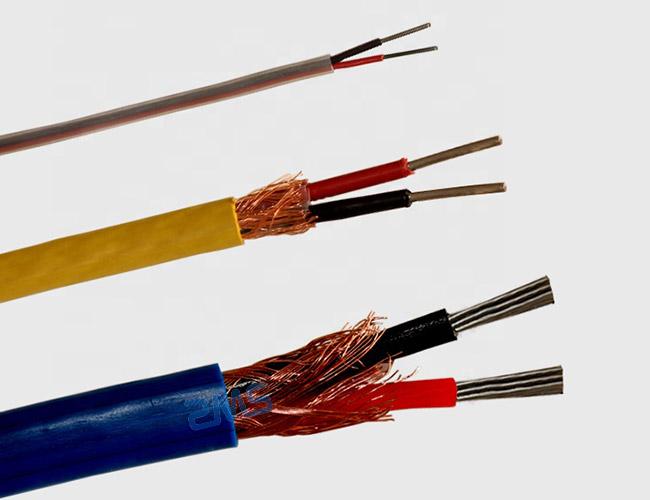
1. What is the precise measurement principle of a thermocouple wire?
The thermocouple wire working principle is based on the Seeback (seeback) utility. That is two different ingredients of the electric conductor on both sides of the combination into a control loop. If the temperature of the two connection ends is not the same, then the physical changes in the control loop are caused by the thermoelectric flow.
A thermocouple cable consists of two different transmission lines (thermoelectric level), one of their ends is electrically welded to the other to produce the precise measurement end of the thermocouple (also known as the working middle end). It is inserted into the substance whose temperature is being measured. The other end of the thermocouple (the control or random end) is connected to the digital display meter. If there is a temperature difference between the exact measuring end of the thermocouple and the control end, the digital display will emphasize the thermally induced electric potential caused by the thermocouple.
2. What is the principle of accurate measurement of RTD?
The RTD is used to accurately measure the temperature of a metal conductor or semiconductor material when there is a temperature change in its own resistance. The part of the RTD that encounters heat (temperature sensor component) is produced by using a thin wire uniformly wound on a frame made of insulating layer material or on a silicon wafer according to the magnetron sputtering process of a laser. When the measured material has a temperature gradient direction, then the measured temperature is the mean temperature of the material layer in the category to which the temperature sensor component belongs.
3. How to choose thermocouple and RTD?
According to the temperature measurement range selection: 500 ℃ above the general selection of thermocouple, 500 ℃ below the general selection of RTD.
According to the measurement accuracy selection: the precision of the provisions of the higher selection of RTD, the precision of the provisions of the low selection of thermocouple.
According to the detection range selection: thermocouple accurate measurement of the general refers to the “point” temperature, and RTD accurate measurement of the general refers to the average temperature of the indoor space.

4. what is called an armored cable thermocouple, what are the advantages?
That is an inorganic mineral insulation thermocouple cable for thermal power plants. The thermocouple level, insulation, and wire sheath according to the overall welding heat treatment and produced, the outer layer seems to be shifted into a layer of “armored cable”, so-called armored cable thermocouple. Compared with the general assembly-type building thermocouple, has the advantages of high-pressure resistance, good bending characteristics, good oxidation resistance, and long service life.
5. What are the index numbers of a thermocouple? What are the characteristics?
The key to the thermocouple index numbers is S, R, B, N, K, E, J, T, and so on. Among them, S, R, and B belong to the precious metal thermocouple, and N, K, E, J, T belongs to the cheap metal material thermocouple.
S indexing characteristics are strong oxidation resistance, suitable for continuous application in a reducing, malleable atmosphere, long-term application temperature of 1400 ℃, and short-term 1600 ℃. Of all thermocouples, the S scale has the greatest level of accuracy and is generally used as the standard thermocouple.
The R scale is basically identical to the S scale except that the heat induction potential is about 15% larger.
The B scale has a very small thermally induced electromotive force at room temperature, so no compensation wire is generally required for accurate measurements. Its long-term application temperature is 1600℃ and 1800℃ in the short term. It can be applied in reducing or neutralizing the atmosphere, and also in short term under vacuum pumping standards.
The characteristics of the N scale are high oxidation resistance at 1300°C, long-term reliability of the thermionic potential and reproducibility of the thermal cycle in the short term, nuclear irradiance resistance, and cold resistance, which can partially replace the S scale thermocouple.
K indexing characteristics are strong oxidation resistance, suitable for continuous application in a reducing, malleable atmosphere, long-term application temperature of 1000 ℃, and short-term 1200 ℃. In all thermocouple application is the most common.
The characteristics of the E index are in the common thermocouple, its thermal induction electromotive force is larger, that is, the sensitivity of the largest. Suitable for continuous application in a reducing, malleable atmosphere, the application temperature is 0-800 ℃.
The characteristics of the J index are used in both reducing atmospheres (application temperature limit 750 ℃), but also in oxidizing atmospheres (application temperature limit 950 ℃), and resistance to H2 and CO vapor corrosion, mostly used in oil refineries and chemical plants.
T scale features the largest accuracy level among all cheap metal material thermocouples, generally used to accurately measure the temperature below 300 ℃.
6. How many ways are there to ground the transformer of RTD? What are the hazards?
There are three methods of transformer grounding for RTD: 2-wire, 3-wire, and 4-wire.
The 2-wire RTD wiring system is easy but brings additional deviation in the wire resistor. Therefore, it is not suitable for manufacturing Class A precision RTDs, and neither the wire nor the transmission wire is suitable for too long in the application.
The 3-wire system eliminates the hazards of wire resistors and has a higher measurement accuracy than the 2-wire system. It is the most widely used as a full process inspection component.
The 4-wire system not only clears the hazards of the wire resistor but also clears the hazards of the resistor when the resistance value of the connecting transmission line is the same. In high precision and accurate measurement, the 4-wire system should be used.
7. What are the advantages and disadvantages of N-type thermocouples versus K-type thermocouples?
Advantages of Type N thermocouples.
K-type thermocouple nickel-chromium alloy in the positive level of Cr, Si elements preferential use of air oxidation caused by the uneven composition of aluminum alloy and thermal induction electric potential drift. In the N-type thermocouple to enhance the Cr, Si composition, the air oxidation of nickel-chromium from internal air oxidation changes to external air oxidation, resulting in redox reactions being carried out only in the surface layer.
This results in good reliability of thermal cycling in the short term at ultra-low temperatures and suppresses magnetic changes.
The N-type thermocouple has eliminated the growth-prone elements Mn and Co from the K type, further enhancing its ability to work against neutron irradiance.
-In the range of 400 ~ 1300 ℃, the N-type thermocouple thermal power plant characteristics of the line are better than the K type.
Defects of N-type thermocouple.
-N-type thermocouple raw materials than K type hard, more difficult to produce processing.
The coefficient of linear expansion of N-type thermocouple is 15% lower than that of stainless steel plate, so the outer casing of N-type armored cable thermocouple should be NiCrSi/NiSi aluminum alloy. -In the -200 ~ 400 ℃ range discrete system deviation is large.
8. how to choose the suitable thermal installation casing?
ASME/ANSI PTC19.3 has sufficient requirements for this matter, and the choice of casing compressive strength analysis system can measure whether the casing design scheme is in accordance with the provisions of the processing process. Installed in the field of thermal casing need to measure the thermal installation
The compressive strength of the tube and the key to endangering the compressive strength of the sheathing tube are the following three points.
1. vibration caused by fluidity: the liquid through the sheath tube causes a certain frequency of vortex, called the vortex area frequency, the frequency of water flow is positively correlated. If this frequency and the resonant frequency of the thermal casing are close or consistent, it will cause co-vibration, so that digestion absorbs a lot of energy, which causes high ground stress and may destroy the thermal casing of the casing inductor.
2. the ground stress caused by mobility: liquid mobility along with water flow and relative density shift, and increased force in the thermal casing, this mobility caused by the working pressure can be obtained according to the measurement.
3. full process working pressure: the thermal casing can bear a large negative pressure can be measured.
The general heat installation casing interface methods are the flange connection type, live sleeve flange type, and welding together three.
9. How to choose the appropriate wear-resistant steel tube thermometer?
When the horizontal installation, select radial or universal ball type wear-resistant steel pipe thermometer.
When installed vertically, select axial or universal spherical wear-resistant steel pipe thermometer.
For skew installation, radial, axial or universal spherical wear-resistant steel pipe thermometers are selected according to specific needs.
If you need to set the upper and lower limit alarm manipulation of the measurement point, you can select the electric contact wear-resistant steel tube thermometer
10. what are the advantages and disadvantages of a wear-resistant steel tube thermometer?
The advantage of a wear-resistant steel tube thermometer depends on the relative cheapness, and reading value visualization, the defect is the temperature measurement scope is small, and the precision is not high relative. Generally as in situ precise measurements, digital display instrument.
11. What are the characteristics of the temperature intelligent transmitter?
The characteristics of a temperature intelligent transmitter are – low loss of static data function, reliability, no maintenance, and long service life.
-Small volumes, can be integrated with thermocouples and RTDs, not only easy to install, but also can save the cost of temperature converter installation.
The transmission of the data signal is a 4-50mA standard data signal, which not only has strong anti-interference and long transmission distance but also can save the expensive compensation wire.
-It can be given in accordance with HART protocol and FF, PROFIBUS system bus communication protocol. 12.
12. What is the precise measuring principle of a working pressure thermometer?
According to the basic law of liquid surging, that is, a certain quality of liquid, under the standard that the volume will not change, the working pressure and temperature of the liquid are linear. Vapor, vapor working pressure, and temperature are also certain functions of the relationship.
Therefore, the working pressure thermometer ruler should be evenly divided into equal parts. The working pressure thermometer is filled with temperature sensor material temperature package, pressure transfer components (capillary), and working pressure photoresistor (torsion reed tube) composition. 13.
13. infrared induction thermometer accurate measurement principle is what?
An infrared thermometer consists of self-collimation, photodetector, signal enhancer, and signal analysis. The output of the signal analysis. Self-collimation of its field of view of the overall target infrared radiation kinetic energy, infrared kinetic energy focus on the photodetector and change into the corresponding electronic signal, the data signal and then calculate the change into the measured overall target temperature value.
14. how to choose the appropriate compensation wire or cable?
Compensating wires and cables for thermocouples are used to increase the thermally induced electric potential of the thermocouple to the secondary instrument panel or main control room. The key has two kinds of compensation wire, broadening type and compensation type, broadening type uses the same raw material as the thermoelectric level, so the precision is higher. The compensation type uses the same raw material as the thermoelectric level with the same characteristics of the thermal potential difference, so the precision is not as high as the broadening type.
15. The difference between RTD and thermocouple
The thermocouple is a kind of temperature measurement sensor, and RTD is like all temperature sensors, but it is different from the RTD key depends on.
15.1 data signal characteristics, the RTD itself is a resistor, and the temperature shifts so that the resistor is caused by a positive or negative resistance value shift. The thermocouple, on the other hand, causes a shift in the induced voltage, which changes with the change in temperature.
15.2 The temperature ranges of the two types of inductors are different. The heat transfer coefficient is generally tested in the temperature range of 0-150 degrees, and the maximum detection range can reach 600 degrees (of course, the negative temperature can be tested).
Thermal coupling can test the temperature range of 0-1000 degrees (or even higher) Therefore, the first one is the ultra-low temperature test, and the latter one is the high-temperature test.
15.3 From the raw materials, the heat transfer coefficient is a metal composite material, with a temperature-sensitive transformation of the metal composite material, the thermal coupling is a bimetallic composite material, both two different metal materials, because of the temperature shift, the potential difference caused on both sides of the 2 different wires.
15.4 PLC matching RTD and thermocouple keying control module is also different, they are no problem, but the general PLC are immediately connected to 4 ~ 50ma data signal, and RTD and thermocouple generally contain intelligent transmitter before connecting to the PLC. if connected to the DCS will not need to use intelligent transmitter! RTD is the RTD data signal, the thermal power plant is the TC data signal!
15.5 PLC also has an RTD control module and a thermocouple control module that can immediately input resistance and thermocouple data signal.
15.6 thermocouples have J, T, N, K, S, and other model specifications, there are more expensive than resistors, and there are also more cost-effective than resistors, but counting the compensation wire, comprehensive engineering costs thermocouple on the high.
RTD is the resistor data signal, the thermocouple is the operating voltage data signal
15.7 RTD temperature measurement principle is based on the electrical conductor (or semiconductor material) resistance with the characteristics of the temperature shift to accurately measure the detection range of negative 00 ~ 500 degrees, common platinum RTD (Pt100, Pt10), copper resistor Cu50 (negative 50-150 degrees).
The thermocouple temperature measurement principle is based on the Seebeck effect to accurately measure the temperature, common are platinum-rhodium – platinum (index number S, detection range 0 ~ 1300 degrees), nickel-chromium alloy – nickel-silicon (index number K, detection range 0 ~ 900 degrees), nickel-chromium alloy – Kang copper (index number E, detection range 0 ~ 600 degrees), platinum-rhodium 30 – platinum-rhodium 6 (index number B, detection range 0 ~ 1600 degrees).