In addition to the main equipment in the photovoltaic system cable power plant construction process, such as photovoltaic modules, inverters, and step-up transformers. In addition to supporting the connection of photovoltaic cable materials to the overall profitability of the photovoltaic power plant. The safety of operation, whether efficient, also plays a vital role, the following is a detailed introduction to the use of common cables and materials in photovoltaic power plants and the use of the environment.
The cable according to the system of the photovoltaic power plant can be divided into DC cable and AC cable, according to the use and use of different environments are classified as follows.
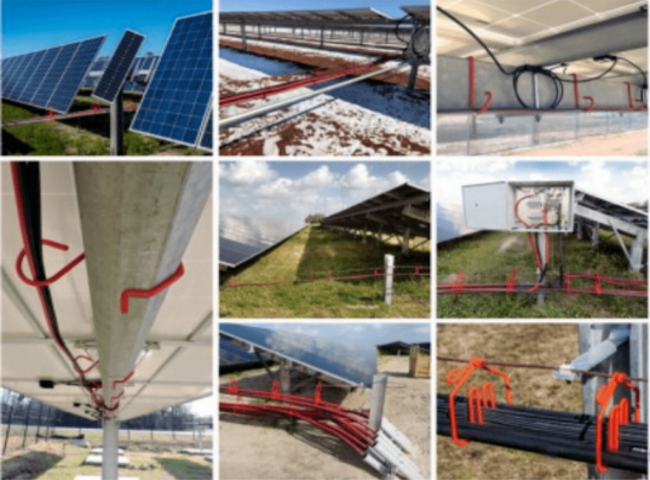
Ⅰ. DC Cables
(1) Series cables between modules and components.
(2) Parallel cables between strings and between their strings to the DC distribution box (sink box).
(3) Cable between the DC distribution box to the inverter.
All the above cables are DC cables, which are laid outdoors more often and need to be moisture-proof, sunlight-proof, cold-resistant, heat-resistant, UV-resistant, and in some special environments, acid and alkali-resistant chemicals.
II. AC Cable
(1) Inverter to step-up transformer connection cable.
(2) Connection cable from the step-up transformer to the power distribution unit.
(3) Connection cable from distribution unit to grid or user.
This part of the cable is an AC load cable, the indoor environment laying more, can be selected by the general power cable selection requirements.
Ⅲ. Photovoltaic Special Cables
In photovoltaic power stations with numerous DC cables to be laid outdoors and in harsh environmental conditions, the cable material should be based on resistance to ultraviolet light, ozone, severe temperature changes, and chemical erosion. Long-term use of cables made of common materials in this environment will result in fragile cable sheaths and even the decomposition of the cable insulation layer. These conditions will directly damage the cable system but also increase the risk of cable short-circuit. In the medium and long term, the possibility of fire or personal injury is also higher, greatly affecting the service life of the system. Therefore, it is necessary to use PV-specific cables and components in PV power plants. PV-specific cables and components have the best weather resistance, UV and ozone erosion resistance, and can withstand a greater range of temperature variations.
IV. Principles Of Cable Design Selection
(1) The voltage withstand value of the cable should be greater than the maximum voltage of the system. Such as 380V output AC cable, to elect the 450/750V cable.
(2) For connections within and between PV arrays, the rated current of the selected cable is 1.56 times the maximum continuous current in the cable obtained from the calculation.
(3) For the connection of AC loads, the selected cable current rating is 1.25 times the maximum continuous current in the calculated cable.
(4) For the connection of the inverter, the selected cable current rating is 1.25 times the maximum continuous current in the calculated cable.
(5) Consider the effect of temperature on the performance of the cable. The higher the temperature, the lower the load capacity of the cable, and the cable should be installed in a ventilated heat sink as much as possible.
(6) Consider the voltage drop should not exceed 2%.
DC circuits are often affected by various adverse factors in operation and cause grounding, making the system not operate properly. Such as extrusion, poor cable manufacturing, insulation material failure, low insulation performance, DC system insulation aging, or the existence of certain damage defects that can cause grounding or become a grounding potential. In addition, the outdoor environment of small animal intrusion or bites can also cause DC grounding faults. So in this case generally use armored, with rodent-proof agent function sheath cable.
Distributed photovoltaic commonly used inverter cable selection.
If the cable length is greater than 50 meters, please refer to the larger size cable.
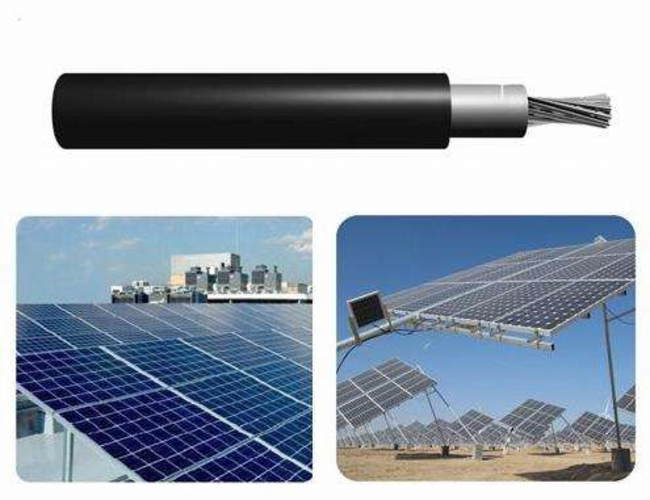
V. Cable Construction Of Photovoltaic Power Generation System
The cost of cable construction in photovoltaic power generation projects is generally large, and the choice of laying method directly affects the construction cost, so reasonable planning and the correct choice of cable laying method is an important part of the cable design work.
1. Cable laying mode according to the engineering situation, environmental conditions and cable specifications, quantity, and other factors to consider, and according to meet the requirements of reliable operation, easy maintenance, and technical and economic principles to choose a reason. PV power generation project DC cable laying mainly has direct burial sand mat brick laying, laying through the pipe, laying in the slotted frame, cable trench laying, tunnel laying, etc.
The laying of AC cables does not differ much from the general power system laying method. DC cable is mostly used between PV modules, between string to DC sink box, and between sink box to the inverter, its cross-sectional area is small and large, usually, the cable is tied along the module bracket or buried directly through the pipe for laying, DC cable in laying generally need to consider.
Precautions for Building PV Cables
(1) Connecting cable between components and connecting cable between string and sink, as far as possible, using the component bracket as a channel to support and fix the cable laying, which can reduce the role of environmental factors to a certain extent.
(2) Cable laying force should be uniform and appropriate, and should not be too tight, photovoltaic sites generally have a large temperature difference between day and night, and should avoid thermal expansion and contraction caused by cable fracture.
(3) In the building surface of the photovoltaic material cable leads, to consider the overall beauty of the building, laying position should avoid laying cables in the sharp edges of walls and brackets, so as not to cut, grind damage the insulation layer caused by a short circuit, or by shear force cut wire caused by a break. At the same time consider cable lines by direct lightning and other issues.
(4) Reasonable planning of cable laying path, reducing cross, as far as possible, combined laying to reduce the amount of excavation during the construction of the project and the amount of cable.
2. Cable connection DC cables in photovoltaic power generation systems are mostly laid outdoors, the connection method is mainly joint plugging, which can be protected by wearing a tube, using the module support as a cable laying channel, and fixed to reduce the impact of environmental factors. Other cable connections and general power systems in the cable connection are roughly the same.
Ⅵ. Difference between DC and AC Photovoltaic System cables
External Structure
Externally, most of the DC PV cables are multi-core, multi-core cable DC frequency is low, and the color division rules are also easy to understand at a glance, for example, the general black on behalf of the A-phase, gray on behalf of the B-phase, blue on behalf of the C-phase, red on behalf of the N-anode, dark blue on behalf of the PE protection pole. AC photovoltaic cable is generally single-core, single-core cable will have a layer of black cladding around it, according to the installation requirements, can be divided according to the different materials, and disconnection length.
Electrical Characteristics and Shock Resistance
DC photovoltaic cable, with high-voltage, anti-bending characteristics, at very high temperatures can still ensure that the cable’s ability to resist the heat line has good insulation properties, can effectively prevent the occurrence of short-circuit fire, extend the service life of the photovoltaic system. The AC PV cable, with good insulation, and anti-aging properties, can also remain intact when impacted, and through molding, can effectively prevent water powder infiltration; but the single-core does not have a high current exchange capacity, so the installation of high-power grade system, according to the actual situation to take the multi-core cable splicing program.
Photovoltaic System Cable Safety
Due to the DC photovoltaic cable core number being higher, and the contact area of the grounding wire being larger, the safety of this type is much higher than the AC photovoltaic cable, and multi-core photovoltaic cables in its resistance to electric strength is slightly lower, and some types of DC cables allow the core temperature of the wire can reach up to 90 ° C. At the same time, it can ensure that the coils themselves with the electrical properties do not change.
Price
Because DC PV cables are equipped with multiple cores, from raw materials to production, relatively speaking, their cost is higher than that of AC PV cables, while AC PV cables use a single core, which costs less.
—ZMS Cable Group