Insulators are a core component in the power transmission system to ensure the safe operation of the lines. Post-insulators and suspension insulators are the two most common insulators used in overhead transmission lines, but there are significant differences in their structure, function, and application scenarios.
In this article, ZMS Cable takes a closer look at the differences and expands on other insulator types, material options, and future technology trends to help engineers and industry practitioners make science-based decisions.
Post Insulators: The Cornerstone of Rigid Support
1.1 Structure and Materials
Post Insulators are usually single-piece rigid structures made of ceramic or silicone rubber. The surface is designed as an umbrella skirt to increase the Creepage Distance to prevent arcing and leakage. Modern post insulators may be made of composite materials for both mechanical strength and weather resistance.
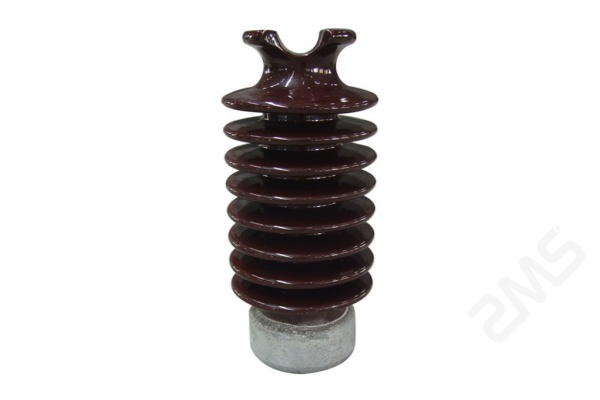
Typical Design Features:
Skirt Arrangement | Multi-layer skirts disperse rainwater, and contaminants and reduce the risk of flashover. |
Metal Attachments | Galvanized steel or aluminum flanges on top and bottom for easy attachment of conductors and grounding structures. |
1.2 Core Functions
Mechanical Support: Carries the weight of the conductor directly, suitable for low voltage (≤1kv) to medium voltage lines (≤33kV).
Electrical Isolation: block current flow from conductors to support structures (such as poles or towers).
Environmental Adaptability: Resistant to ultraviolet rays, salt spray, and industrial pollution, suitable for stable climate areas.
1.3 Application Scenarios
Distribution Network: low and medium voltage transmission lines in urban and rural areas.
Substation: Isolation busbar, circuit breaker, and other equipment.
Railroad Electrification: contact network support to ensure the safety of the train power supply.
Suspended Insulators: Flexible Options for High Voltage Systems
2.1 Structure and Materials
Suspended insulators consist of multiple insulating disks in series, common materials include:
Porcelain Insulating Discs: traditional material, low cost but brittle.
Glass Insulating Discs: Self-bleeding characteristics for easy fault detection and maintenance.
Composite Insulators (Silicone Rubber): lightweight and highly resistant to dirt flashover, suitable for harsh environments.
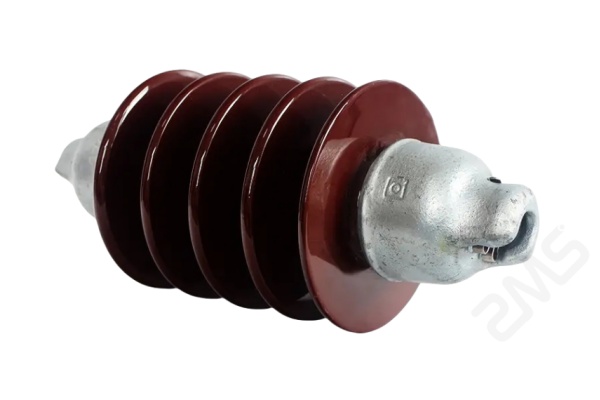
Typical Design Features:
Disc connection | Flexible suspension chain by Ball-and-Socket or U-groove links. |
Pressure Equalizing Ring | Balance the electric field distribution in UHV lines to reduce corona discharge. |
2.2 Core Functions
Dynamic Load Adaptation: Swing freely with wind or temperature change to avoid mechanical stress concentration.
High Voltage Isolation: for 66kV and above transmission lines, up to 1200kV.
Anti-Flicker Performance: The water-repellent surface of the composite insulator can effectively resist rain, snow, and salt spray pollution.
2.3 Application Scenarios
Ultra-High Voltage Transmission (EHV): such as the main line of the national grid.
Cross-Sea or Desert Areas: composite insulators are highly corrosion-resistant and adaptable to extreme environments.
Seismically Active Zones: flexible structures can absorb vibration energy and reduce the risk of rupture.
Post Insulators vs. Suspended Insulators: 6 Key Differences Comparison
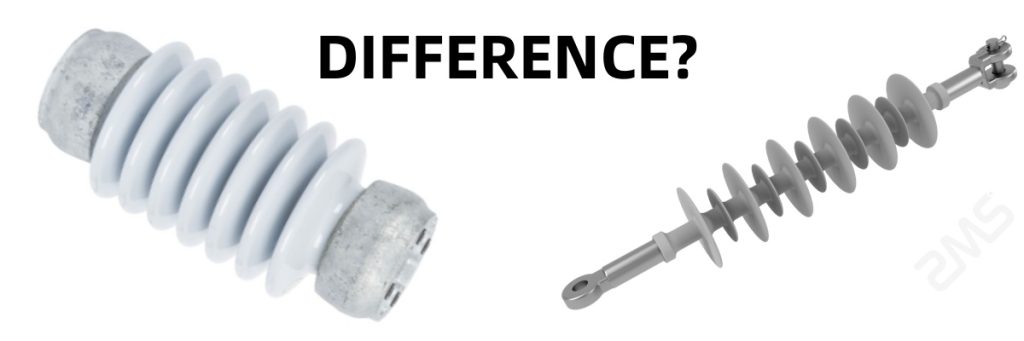
Comparison Dimension | Post Insulators | Suspension Insulators |
Machine Structure | Rigid single piece, vertically mounted | Flexible multi-disc chain, horizontal suspension |
Voltage Level | ≤33kV | ≥66kV (up to 1200kV) |
Anti-flashing Ability | Umbrella skirt dependent design for low contamination areas | Water-repellent surface of composite insulators, suitable for highly polluted and humid environments |
Maintenance Costs | High overall replacement cost | Individually replaceable damaged disks for flexible maintenance |
Seismic Performance | Weak seismic capacity | Flexible structure absorbs vibrations and is resistant to earthquakes |
Economics | Low initial cost with a lifespan of about 20 years | High initial investment, but life expectancy of up to 40 years (composite insulators) |
Other Common Insulator Types and Their Applications
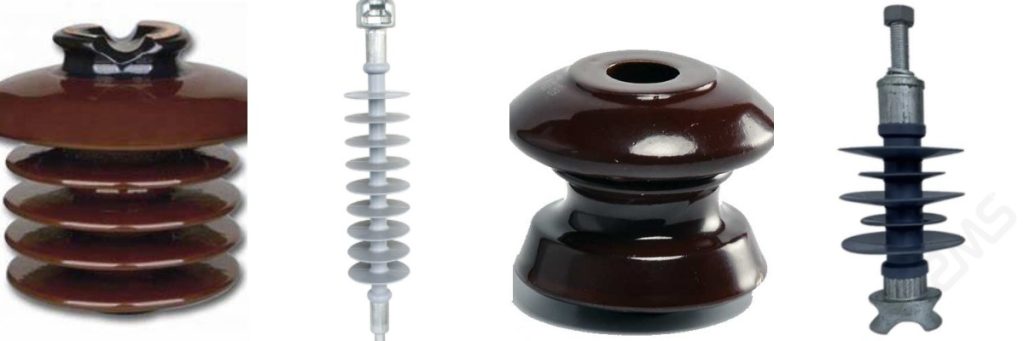
4.1 Pin Insulators
Structure: Umbrella skirt with threaded pins at the top, fixed to wooden or concrete poles.
Application: Distribution lines below 11kV, widely used in rural power grids.
4.2 Composite Long Rod Insulators (Composite Long Rod Insulators)
Material: fiberglass mandrel + silicone rubber skirt, without the risk of porcelain brittleness.
Advantage: light weight (only 1/10 of porcelain), strong impact resistance, suitable for high-speed rail contact network.
4.3 Butterfly Insulators (Shackle Insulators)
Structure: Central perforated design, fixing the conductor by bolts.
Application: Corners or terminals of low voltage lines, low cost but easy to deteriorate.
4.4 HVDC Insulators
Special Requirements: More serious dirt accumulation under the DC field, needs a larger creepage distance, and special materials.
Example: ZMS Cable supplied silicone rubber composite insulators to Uruguay for the ±800kV UHV DC retrofit project.
Technical Evolution and Selection of Insulator Materials
5.1 Traditional Materials: Ceramic and Glass
Ceramic Insulators: low cost but bulky and susceptible to “cold bursts” (sudden temperature changes).
Glass Insulators: Self-bleeding characteristics facilitate inspection, but can cause short circuits when broken.
5.2 Composite Materials: Silicone Rubber Revolution、
Hydrophobic: water beads on the surface instead of a film, dramatically reducing the probability of dirt flash.
Lightweight: reduce the tower structure load, and reduce installation costs.
Case: Composite insulators are widely used in Nordic countries to cope with snow and ice environments.
5.3 Future Trends: Intelligent Insulators
Sensor Integration: real-time monitoring of leakage current and mechanical stress to prevent failure.
Self-Cleaning Coating: Photocatalytic materials decompose surface pollutants, reducing maintenance frequency.
What does ZMS think about choosing the right insulator?
Evaluating Voltage Levels | Low voltage distribution: pin or post insulators. |
Ultra High Voltage Transmission: Suspended Composite Insulators. | |
Analyzing Environmental Conditions | Coastal/industrial areas: Prefer silicone rubber composite insulators. |
High altitude: increase the number of parachute skirts to cope with low-pressure discharges. | |
Considering Economics | Short-term project: cost reduction for ceramic or glass insulators. |
Long-term operation: investing in composite insulators reduces life cycle costs. | |
Compliance Check | Conforms to IEC 60383 (international standard) or GB/T 19519 (Chinese national standard). |
Post insulators and suspension insulators have their advantages and disadvantages, and the rise of composite materials is redefining the industry standard for accessory insulators in the future. In the future, with the popularization of smart grid and ultra-high voltage technology, insulators will be developed in the direction of lighter weight, intelligence, and environmental adaptability, ZMS believes that project engineers need to follow the technology trend and choose the optimal solution according to the specific needs to achieve the high efficiency and safety of the power system.