In recent years, as countries have increased their investment in the energy sector, the investment in energy construction has been increasing, and the demand for energy production safety will become more urgent on a global scale. An offshore oil platform is one of the main facilities for offshore oil extraction and one of the main facilities used for onshore oil drilling platforms.
An oil rig is one of the main platforms for oil and gas exploration and development and is a facility used by offshore oil fields for extraction and production operations. The equipment of the drilling platform, including drilling, completion, gas extraction, extraction, and water injection, is carried out offshore in a harsh and intensive operating environment.
If the well is often kept at a lower temperature, the production process must meet special requirements such as cable performance and environmental temperature stability requirements.
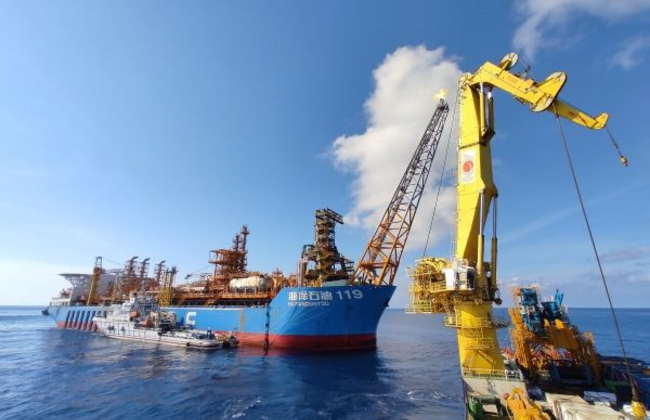
I. Offshore oil platform with cable technical requirements
The cable used in the offshore oil platform needs to have high temperature and seawater resistance, and the physical properties of the insulation layer and corrosion resistance need to meet the national standard requirements.
At present, among the domestic standards, only GB/T9853-2014 “Cable for Offshore Oil Platforms” meets the technical requirements for cables used on offshore oil and gas platforms, and most of the other standards are recommended standards.
In this paper, the conditions of use and ambient temperature stability requirements of power cables for offshore oil exploration platforms are described. The standard specifies the requirements of each index and analyzes and compares the IEC/T 16601-2012 “Conditions of Use for General Electric Equipment for Offshore Oil and Gas Platforms” and the European IEC 62382-2005 “Voltage and The performance indexes required in IEC 62382-2005 “Voltage and Frequency Range of Offshore Gas Terminal Equipment” were analyzed and compared according to the standard. At the same time, the implementation rules of the two national standards are compared.
The above-mentioned provisions are less related to the production process to meet the specific requirements of the cable but can be adjusted through the production process parameters and other means to make the product meet the relevant performance indicators while better meeting the needs of different environmental temperatures.
1. High-temperature resistance
High-temperature resistance is a relatively important performance indicator of the offshore oil exploration platform with the cable, the indicators are at high temperatures on the comprehensive impact of the resistance of the cable insulation layer.
Because the cable will form a certain protective layer on the inner wall of the insulation layer during operation, thus effectively reducing the insulation short circuit and other fault phenomena in high-temperature environments. Therefore, the high-temperature resistance of the power cable for offshore oil exploration platforms is particularly important.
At the same time, its production process also needs to be reasonable arrangements for cable structure design, to ensure effective control of performance indicators in different temperatures, stability, and reliability.
Therefore, the standard stipulates that: the power cable materials for offshore oil exploration platform heat resistance tests should be in line with the requirements of the high-temperature test protection layer materials, and cable core materials should not exceed 10 kVA.
2. Seawater resistance
GB/T9853-2014 “offshore oil platform with cable”, for the cable in the temperature range of 10 ℃ -40 ℃ (do not consider in seawater) for work or long operation process, the insulation layer of moisture resistance should meet the IEC/T 16601-2012 “offshore oil and gas platform general electric equipment conditions of use” clearly put forward ” The cable can work in the sea for a long time when the working temperature is not higher than 40℃”. This is consistent with the current technical requirements for the use of offshore oil and gas field equipment outside China’s waters.
Through the study, it is found that harsh sea conditions or large temperature changes will lead to changes in the thermal conductivity of the material and will lead to local overheating of the cable. At the same time, the material properties of the insulation layer and the material resistivity vary greatly under different sea conditions.
The heat generated during severe sea conditions will lead to localized overheating of the cable material, resulting in insulation failure. Therefore, the insulation and cables for marine equipment need to have good anti-aging performance in sea conditions to reduce the thermal impact on the cables.
GB/T9853-2014 “offshore oil platform cable” clearly put forward the “cable in the specified maximum temperature thermal operating temperature range after 1 year of operation, the product should be completely heated loss” of the relevant requirements, the cable in the premise of meeting the above requirements can be extended for 10 months of operation.
The standard can be based on the actual production conditions to choose the appropriate sea conditions on the number of times the cable can be run in the specified time and the stability of cable products under sea conditions to meet the requirements.
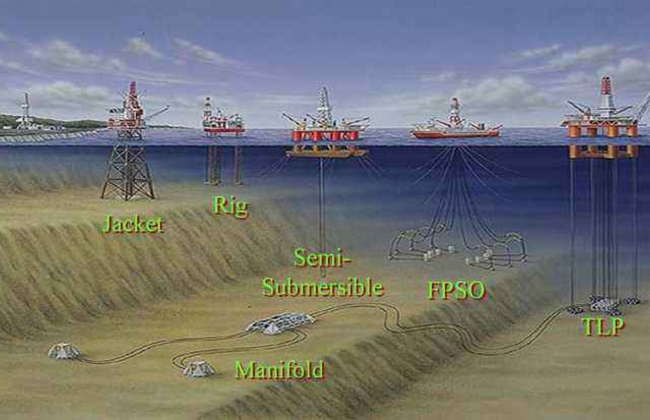
II. Product characteristics, technical indicators
JTG04-200-2004 offshore oil platform cable is a new type of marine cable designed based on the traditional marine cable, mainly suitable for installation on offshore oil drilling platforms for drilling operations.
As there are many pieces of equipment on the offshore oil platform, different equipment have different requirements for power supply and transmission, therefore, it is necessary to choose the marine cable with high requirements for environmental temperature stability.
The cable is made of high carbon alloy steel with good high-temperature performance, smooth surface, and high tensile strength and flexural strength.
Higher tensile strength and flexural strength and better bending resistance, suitable for laying in a variety of special environments.
Good electrical properties (good abrasion resistance, insulation resistance value of 0) as well as good mechanical properties (good impact resistance, insulation resistance value of 0).
Lower elongation at break (break wire direction is approximately equal to the length at the break) as well as an excellent electrical performance at higher temperatures and stable performance in harsh environments (ocean temperatures above 0°C, service life of about 20 years).
The dimensional tolerance requirements are a length of 2 m×1 m, a width range of 0.02~0.4 m, a wall thickness of 0.3~0.5 mm; insulation resistance value of 0.100~1 kv/m- h.
1. This product adopts flame retardant and high-temperature resistant PVC insulation material, and its insulation performance, electrical performance, and mechanical performance indexes meet the requirements of GB/T10770-2008 “Offshore (well) oil power cables and cable accessories”.
This product, as a high-performance submarine cable, is of great significance in preventing leakage and corrosion on offshore oil platforms and improving service life.
From the perspective of the ambient temperature, the insulation performance of the cable will be affected when the sea temperature is higher than 0℃, and the service life is about 20 years. In addition, the sea’s high temperature and high humidity environment also have a certain impact on the corrosion resistance of the cable.
Therefore, the product must have the advantages of heat resistance and high strength to be suitable for use and maintenance on offshore oil platforms.
From the point of view of submarine cable technology, there are only a few domestic enterprises that have independent research and development strength and have achieved more perfect results.
For example, South Korea Daewoo (China) company introduced a set of foreign advanced technology in the production process, solved the previous heat and high and low-temperature insulation problems, and the product life reached an internationally advanced level.
To meet the needs of users, the company has also developed a variety of new products.
2. The product has physical and chemical indexes such as flame retardancy, temperature resistance, and mechanical, weathering, and impact resistance.
This product conforms to the provisions of GB/T7233-1996. GB7011-2011 The technical conditions of cables for petrochemical equipment JTG04-200-2008. The operating temperature of the wire and cable is 0℃~40℃. This product is suitable for cables used for laying and using on offshore oil platforms and has good weather resistance (5℃~50℃) such as UHTS submarine cables.
JTG04-200-2008 stipulates that: insulation and sheathing materials must meet the requirements of GB/T7233-1996 quality standards.
Sheathing materials must be corrosion and aging-resistant.
It should have good weather resistance and mechanical properties in a wet environment.
The use temperature of this product should be 0℃~40℃, use range (sea condition): temperature range 0~40℃, temperature duration more than 5 hours (special area).
This product can not exceed 4 h. Flame retardant materials should have flame retardancy, high-temperature resistance, weather resistance, and good mechanical properties.
Rubber material should have aging resistance, good mechanical properties, good elasticity as well as impact resistance.
The product should not be run under high temperatures and a corrosive environment for a long time (the oxygen content in sea conditions and the atmosphere should not exceed 0.5%).
The product shall not be exposed to oxidizing agents, acids and bases and other harmful substances, etc. The main insulation material of the cable also includes two styles of the metal sheath and non-metal material sheath.
3. This product is made of high carbon alloy steel material, which has high strength and ability to bear a heavy load and is not affected by temperature and stress corrosion.
It is suitable for outdoor laying in a harsh environment, especially in cold areas.
Our company has perfect testing means and testing equipment, which can meet the requirements of field use and provide high-quality test data.
The products have excellent electrical and mechanical properties; insulation resistance value 0.100~1 kv/m- h.
The insulation sheath thickness is 0.3 mm.
4. The product adopts advanced production technology and processing equipment, and the production process adopts several advanced technologies such as online automatic control process technology, online automatic testing production line, and intelligent monitoring system to ensure reliable and controllable product quality.
The product adopts advanced production equipment, advanced processing technology, and stable quality.
The product products have reliable performance, complete specifications, and beautiful appearance, suitable for use on offshore oil drilling platforms, and suitable for installation in various special weather environments.
The products have good insulation and sheathing protection, safety, reliability, and good aesthetics. The products have good temperature resistance as well as excellent mechanical properties.
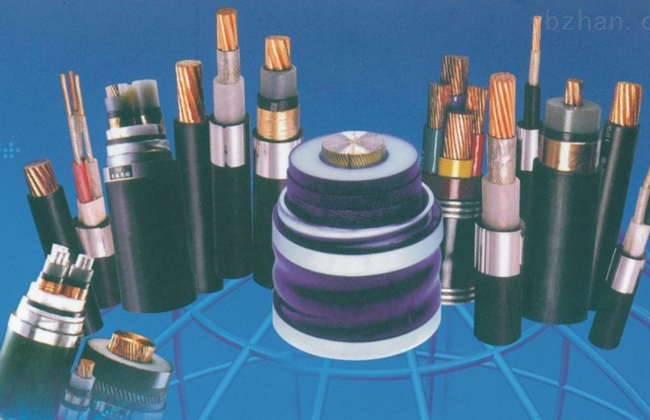
III. Scope of application
The cables used for power supply on offshore drilling platforms are generally copper-core or aluminum-core power cables. Offshore drilling platform cables are generally copper-core or aluminum-core power cables, which contain more copper with high impurity content.
For long-term use in high and low-temperature environments and seawater environmental conditions, the cable has good corrosion resistance as well as good mechanical properties, but due to the high salinity of marine seawater and the need to prevent the wire from moisture corrosion, there is greater applicability.
As the cable on the offshore drilling platform can not be directly applied to the high-temperature state, so it has a high resistance to seawater corrosion performance.
1. Cables on offshore oil platforms
With the exploitation of offshore oil, the requirements for oil field development are getting higher and higher. To ensure the normal operation of the drilling platform and other equipment, the working temperature of the cable must be reduced to below 25℃.
Cables for offshore oil platforms use copper core copper wire and aluminum core copper wire. The main features of copper core and aluminum core copper wire in high and low-temperature environments are good resistance to seawater corrosion, low insulation resistance, good impact resistance, low price, and reasonable cost performance.
Under normal operating temperatures, copper-core and aluminum-core single-core cables have better ozone resistance (UOE) performance than ordinary wires and cables because the cables have good resistance to the ozone environment. And for UOE performance characteristics, the offshore oil platform used is UOE + HDPE combined cable structure system that is UOE + HDPE + SPE + TPE = UP- HDPE + XPE type cable structure form, where TPE can be used as a single cable in high and low-temperature environment structure form; and SPE as four multi-core cable composition of the overall structure form can meet the extreme temperature (UOE+ HDPE) under extreme temperature conditions. Since the selection of cables for offshore oil platforms requires the selection of different types of cable solutions for construction and installation operations, different types of cables should be selected for construction and installation on offshore oil platforms. During use, attention should be paid to prevent the cable from being eroded by seawater or moisture, so that the cable is damaged and deformed and the insulation performance is reduced.
2. The offshore platform and the cable used on the platform
Offshore platforms with the cable, generally choose low smoke halogen-free flame retardant submarine cable, requiring materials with excellent corrosion resistance, abrasion resistance and crack resistance, and other related indicators.
Cables and submarine oil and gas pipelines share a submarine cable trunk, and need to use sulfur-resistant, chemical corrosion-resistant flame retardant wire and cable.
Offshore oil platforms and land-based oil and gas pipelines share an onshore oil and gas pipeline trunk line, which also requires the use of sulfide-resistant, chemical corrosion-resistant, and corrosion-resistant submarine cable trunk lines.
Subsea oil field operations need to be carried out in a relatively closed area and share a set of drilling fluid delivery systems with land-based oil drilling equipment, which needs to meet the requirements of up to 10 years or even longer service life.
IV. Operating Environment and Conditions
When working on offshore drilling rigs, they need to operate in the sea all year round, and the working environment is harsh, requiring good resistance in the range of -50℃~+60℃.
Equipment components (such as offshore oil rigs) are usually characterized by excessive weight and complex structure, high material requirements for the equipment, often harsher use environment, and relatively high requirements for cable performance.
Each piece of equipment on a ship requires a different type of cable, and different types of cables are required depending on production and installation conditions.
The offshore cables used in offshore oil rigs are mainly divided into two types submarine optical cables (OTN) and onshore cables by submarine cables and oil cables.
Submarine fiber optic cables are further divided into three types: ordinary cables, marine cables, and special cables.
As the submarine fiber optic cable in the submarine cable accounted for a relatively large, in general, the marine cable in marine operation of more types of cable is required, such as submarine cable, stranded wire, etc.
At the same time, to ensure good anti-corrosion performance, and anti-aging effect and extend the service life, in addition, to ensure that the operating conditions of offshore oil rigs, but also the use of submarine fiber optic cable conditions and environmental conditions require special requirements.
1. Submarine cable used in a high-temperature environment
As a large number of harmful gases are generated during the extraction of offshore crude oil and natural gas, all equipment components on offshore oil platforms are exposed to high temperatures and humidity for a long time.
High temperatures and humidity can accelerate corrosion inside and outside the cable, so to ensure the long-term use of the equipment, the cable is generally required to be able to withstand high temperatures and corrosion under normal operating conditions at sea.
But for the high-temperature environment required for the cable, due to its special characteristics, its high-temperature resistance is far below the performance indicators of ordinary submarine cable.
Therefore it is a very important and necessary requirement when the temperature of the offshore oil rig reaches above 70℃.
When using submarine cables in high-temperature environments, in addition to meeting the above requirements also need to ensure good wear and corrosion resistance, irradiation resistance, anti-aging performance, and resistance to atmospheric corrosion performance.
2. Salt spray corrosion environment of the use of submarine cable
Submarine cable is generally used in salt spray corrosion environment, its salt spray corrosion environment, usually using the impregnation method of treatment and insulation modification methods to enhance the ability of the cable to resist salt spray during use.
Specifically, the first is the use of organic salt spray coatings or chemical salt spray coatings on submarine cables, which usually have a strong anti-corrosion ability.
The next step is to apply the coating at a salt spray concentration of 5 mg/L, which also has excellent resistance to salt spray penetration.
The last is the use of special submarine cables with salt spray protection ability and salt spray erosion resistance.
For the salt spray corrosion environment used in the submarine cable, it needs to have good salt spray penetration resistance and good anticorrosive performance of the submarine cable; at the same time, contact with corrosive media should be avoided as much as possible.
After the laying of the submarine cable covered with salt spray; at the same time avoid exposure of the submarine cable to a high salt spray environment, or in other harsh environments using chemical protection.
In general, the surface of ordinary submarine cable will go through a layer of oxide film to protect the cable.
At the same time, the effective isolation of seawater and salt spray is also a very important part.
—ZMS Cable Team