With the development of the cable industry, the advantages of copper-core cable are more. Copper-core cables occupy an absolute advantage over aluminum-core cables in the cable market. However, the high price of copper-core cable also caused an increase in production costs, and also bad construction. The aluminum-core cable as a cable industry “foreign army” emerged, in the market’s favor.
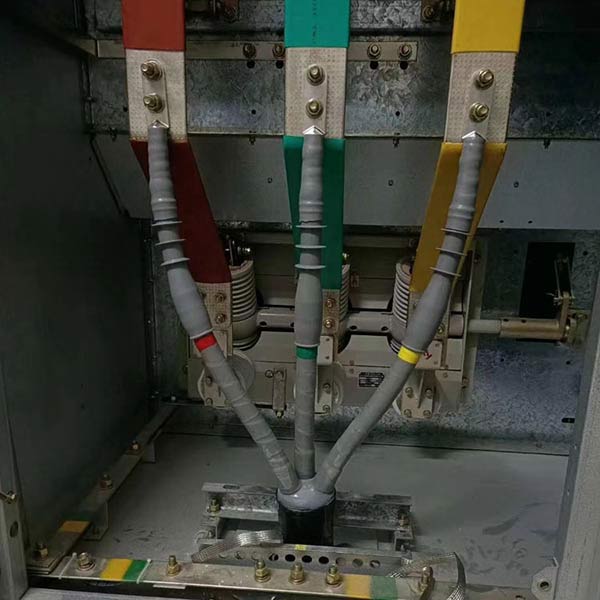
Compared with the traditional copper-core cable, what are the outstanding advantages of aluminum alloy cable?
1. Electrical conductivity — In general, ordinary aluminum-core cable and wire are 2 to 4 specifications larger after the same electrical conductivity as copper-core cable and wire. But the aluminum alloy cable uses a tight compression stranding technology so that the conductor compression degree of 93% to 95%. Thus, the outer diameter of the cable is greatly reduced. According to reliable data, for the same electrical performance, aluminum alloy cable only needs to be one model larger than copper core cable specifications.
2. Mechanical performance — bending performance First, aluminum alloy cable because of the adoption of new technology makes its flexibility can be greatly improved, compared with the corresponding copper-core cable, its flexibility increased by nearly 30%. Secondly, the bending radius of the aluminum alloy cable is 7 times the outer diameter, while the corresponding copper core cable can only do a minimum of 10 times the outer diameter. Thirdly, the bounce performance of aluminum alloy cable is 40% smaller than that of copper core cable, and aluminum alloy cable has no memory, so its bounce performance is obviously better than that of copper core cable. Finally, in the process of cable laying, aluminum alloy cable is more conducive to installation and compression at the terminal head, which improves the stability at the terminal.
3. Corrosion resistance — The main component of aluminum alloy cable is aluminum, which can easily form a dense oxide film in the air, which prevents the metal inside the cable from being further oxidized. While copper core cable will not create an oxide film, after the surface of the cable is oxidized. It will further oxidize the internal metal when after a period of time, the surface oxide of the copper core cable falls off. And then it will be re-oxidized in a new round, resulting in a metal loss. During the manufacturing process, aluminum alloy cable is added with rare metals to further improve the corrosion resistance of aluminum alloy cable and reduce the potential difference between different metals. Studies have shown that the 5XXX type series aluminum alloy, in the seawater environment, does not produce significant corrosion phenomena.
4. Connection performance — The alloy composition in the aluminum alloy cable greatly improves the connection performance of the aluminum alloy cable. The high creep resistance of aluminum alloy cable makes it overloaded for a certain period of time. Overheating can also ensure the stability of the connection. Aluminum alloy cable is equipped with special copper and aluminum over terminals using a friction welding process, with high weld strength, good electrical conductivity, resistance to galvanic corrosion, etc., to better ensure the reliability of its connection.
5. Economic performance — The material cost of aluminum alloy cable is significantly lower than that of copper core cable, and it is calculated that the material cost savings of aluminum alloy cable can be more than 20% compared with copper core cable according to the similar electrical performance. Due to the lightweight aluminum alloy cable, high mechanical strength, small turning radius, small recoil flexibility, and other characteristics. Therefore, the aluminum alloy cable has a flexible installation method, which can be used along the wall to lay open and can also be installed using cheaper ladder frames instead of bridges. Therefore, the installation cost can be saved by 30% to 40% on average. Likewise, due to the characteristics of aluminum alloy cable, which makes its installation flexible and light, it can save a lot of labor costs, and according to statistics, aluminum alloy cable can reduce more than 40% of working days.
From these five advantages, we can see that the use of aluminum alloy cable greatly reduces the cost of finished product protection and site care in the process of construction and use
So, now there is a question, can I use bimetallic cable lugs to connect aluminum alloy cables? Give you five reasons to choose aluminum alloy special terminals
The first big reason: is copper and aluminum transition terminals due to the presence of aluminum in the terminal lugs, all the defects and shortcomings of aluminum problems still exist. This cable terminal is used to connect aluminum alloy cable, the advantages and value of aluminum alloy cable are gone, it is better to use an aluminum cable directly because the aluminum cable is more economical. The use of an aluminum alloy special terminal can give full play to the advantages and value of aluminum alloy cable.
The second reason: is copper and aluminum transition terminal lugs because the original is used to connect the aluminum cable, terminal installation size and terminal equipment size do not match. Not only increase the cost of transferring copper plates, etc. but transferring copper plates to multiple transfers, will also leave connection security risks. The use of aluminum alloy special terminals can avoid similar problems.
The third reason: is that the copper and aluminum cable lugs and electrical terminal lugs do not match, increasing the cost of transferring copper plates and often producing contradictions. So much so that it is difficult to avoid the connection safety hazards caused by the brutal construction that occurs because such problems cannot be solved. The use of an aluminum alloy special terminal can avoid similar issues.
The fourth reason: is bimetallic cable lugs because the original is used to connect the aluminum cable, the inner diameter of such terminals and the cable conductor’s outside diameter does not match. You must use special crimping tools, resulting in difficulty to regulate the construction, leaving connection safety hazards. The use of aluminum alloy special terminals can avoid similar problems.